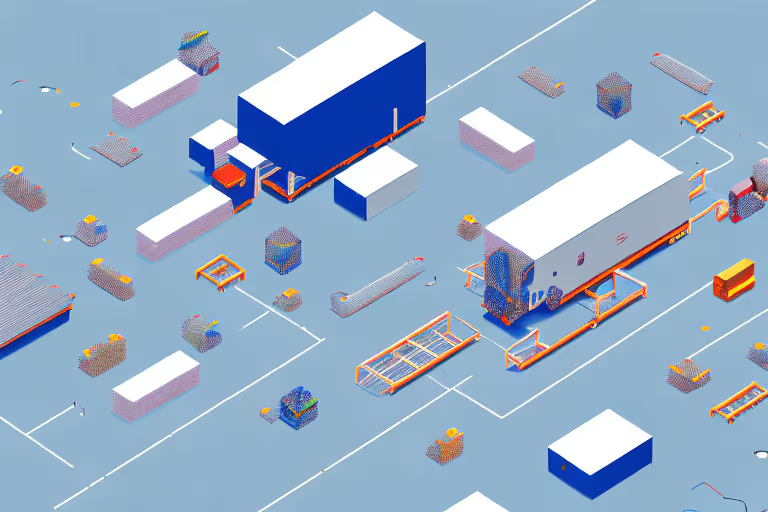
In this article, we will explore the various technologies that can be used to fulfill orders and how they have revolutionized the way businesses handle their operations.
Detailed Look at Specific Order Fulfillment Technologies
Let's take a closer look at some specific technologies that have had a significant impact on order fulfillment:
Warehouse Management Systems (WMS)
A Warehouse Management System (WMS) is a software application that helps businesses manage warehouse operations effectively. WMS automates processes such as inventory tracking, order picking, and packing, allowing for greater accuracy and efficiency.
It provides real-time visibility into inventory levels, streamlines order processing, and optimizes warehouse layout and space utilization.
Order Management Systems (OMS)
An Order Management System (OMS) is a centralized software platform that enables businesses to manage their entire order fulfillment process.
OMS integrates various systems, such as inventory management, order processing, and shipping carriers, into a single interface, providing a seamless experience for both businesses and customers. With an OMS, businesses can streamline order processing, track orders in real-time, and manage customer communication effectively.
Inventory Management Software
Inventory Management Software helps businesses keep track of their inventory levels accurately. It provides real-time visibility into stock levels, alerts businesses when inventory needs to be replenished, and automates the order fulfillment process.
Inventory Management Software prevents stockouts and overstocks, ensuring that businesses can fulfill customer orders promptly and efficiently.
Robotics and Automation in Order Fulfillment
The use of robotics and automation in order fulfillment has gained significant popularity in recent years. Robots can take over repetitive and time-consuming tasks such as picking and packing, reducing human labor and increasing accuracy. Automation technologies, such as conveyor systems and sorting machines, can streamline the entire order fulfillment process, allowing businesses to handle a higher volume of orders with fewer errors.
Case Studies of Successful Technology Implementation in Order Fulfillment
Several businesses have successfully implemented technology in their order fulfillment operations, revolutionizing the way they handle their processes and meet customer demands. Let's take a look at a couple of case studies:
Amazon's Use of Robotics in Order Fulfillment
Amazon, the e-commerce giant, has heavily invested in robotics to optimize their order fulfillment process. Robot assistants work alongside human employees in their warehouses, increasing picking and packing speed, and improving overall efficiency.
Amazon's use of robotics has allowed them to handle a massive volume of orders and provide fast and accurate deliveries to their customers.
How Zara Optimized Their Order Fulfillment with Technology
Zara, a global fashion retailer, utilizes technology to streamline their order fulfillment process. They leverage Inventory Management Software, allowing them to track inventory levels in real-time and prevent stockouts.
Furthermore, they use RFID (Radio-Frequency Identification) technology to improve inventory accuracy and automate stock replenishment, ensuring that they can fulfill customer orders promptly.
Technological Innovations in Order Fulfillment
Recognizing the need for a more efficient and accurate order fulfillment process, businesses turned to technology for solutions. The advancements in technology have revolutionized the way businesses handle their operations, enabling them to meet customer demands and scale their operations effectively.
Overview of Order Fulfillment Technologies
A variety of technologies have emerged to streamline the order fulfillment process. Warehouse Management Systems (WMS), Order Management Systems (OMS), Inventory Management Software, and robotics and automation are just a few examples.
These technologies work together to optimize inventory accuracy, improve order processing speed, and enhance the overall efficiency of order fulfillment.
Warehouse Management Systems (WMS) play a crucial role in order fulfillment. They provide real-time visibility into inventory levels, allowing businesses to effectively manage stock and prevent stockouts.
WMS also enable businesses to track the movement of goods within the warehouse, ensuring efficient picking, packing, and shipping processes. With the help of WMS, businesses can achieve higher inventory accuracy rates, reduce order errors, and improve customer satisfaction.
Order Management Systems (OMS) are another essential technology in order fulfillment. OMS centralizes order processing, allowing businesses to efficiently manage and track orders from multiple sales channels.
OMS automates various order management tasks, such as order entry, order routing, and order tracking. By streamlining these processes, OMS helps businesses reduce order processing time, minimize errors, and improve order fulfillment speed.
Inventory Management Software is a critical component of order fulfillment technology. It provides businesses with real-time visibility into inventory levels across multiple locations, enabling them to optimize stock levels and prevent overstocking or stockouts.
Inventory Management Software also automates inventory replenishment, ensuring that businesses have the right products available at the right time. By efficiently managing inventory, businesses can reduce carrying costs, improve order fulfillment speed, and enhance customer satisfaction.
Robotics and automation have also made significant contributions to order fulfillment. Automated picking systems, such as robotic arms and automated guided vehicles (AGVs), have revolutionized the picking process in warehouses.
These technologies can pick and pack products at a much faster rate than manual labor, significantly increasing order processing speed. Additionally, robotics and automation can minimize errors and reduce the physical strain on warehouse workers, leading to improved productivity and employee satisfaction.
Benefits of Using Technology in Order Fulfillment
The benefits of implementing technology in order fulfillment are immense.
- Firstly, it allows for real-time visibility into inventory levels, enabling businesses to manage stock effectively and prevent stockouts. With accurate and up-to-date inventory information, businesses can fulfill customer orders promptly, avoid backorders, and maintain high customer satisfaction.
- Secondly, technology automates several manual tasks involved in the order fulfillment process. Manual tasks, such as data entry, order processing, and inventory tracking, are prone to human errors. By automating these tasks, businesses can minimize errors and improve overall efficiency. With fewer errors, businesses can reduce order fulfillment time, decrease the number of returns and exchanges, and enhance customer trust and loyalty.
- Lastly, technology provides valuable data and analytics that businesses can leverage to optimize their order fulfillment processes. By collecting and analyzing data on order volumes, order patterns, and customer preferences, businesses can make data-driven decisions to improve their operations. For instance, understanding and managing the fulfillment cost per order can significantly impact profitability. With continuous improvement based on data insights, businesses can enhance order fulfillment speed, accuracy, and customer satisfaction.
For example, they can identify popular products and adjust their inventory levels accordingly, or they can identify bottlenecks in the order fulfillment process and implement process improvements. With continuous improvement based on data insights, businesses can enhance order fulfillment speed, accuracy, and customer satisfaction.
Understanding Order Fulfillment
Before diving into the technological advancements in order fulfillment, let's first establish a basic understanding of this process. Order fulfillment encompasses everything from inventory management to shipping and delivery. It involves multiple steps, such as order processing, picking and packing, and last-mile delivery.
Order fulfillment is a critical aspect of any business operation. It is the process that ensures customers receive their ordered products in a timely and accurate manner. Without efficient order fulfillment, businesses risk losing customers and damaging their reputation.
The Basics of Order Fulfillment
At its core, order fulfillment begins when a customer places an order. This can be done through various channels, such as a website, phone call, or in-person at a physical store. The order is then processed and validated, ensuring that all necessary information is correct and complete.
Once the order is confirmed, the picking and packing process begins. This involves selecting the items from the inventory and carefully packaging them for shipment. It is crucial to accurately pick the right products and ensure they are securely packed to prevent any damage during transit.
After the picking and packing process is completed, the order is ready for shipment. The chosen shipping method will depend on various factors, including the customer's location, shipping preferences, and the urgency of the delivery. The order is then dispatched to the customer's desired location.
The Importance of Efficient Order Fulfillment
Efficient order fulfillment is crucial for businesses to thrive in today's competitive market. Customers have come to expect fast and accurate deliveries, and failure to meet these expectations can result in lost sales and damaged reputation.
Implementing the right technology can significantly improve the efficiency of order fulfillment. For example, the use of automated systems for order processing can streamline the validation and confirmation process, reducing the chances of errors.
Advanced inventory management software can help businesses keep track of their stock levels, ensuring that popular items are always available for quick fulfillment.
Last-mile delivery, the final leg of the order fulfillment process, is often the most challenging and time-consuming. Implementing route optimization software can help businesses plan the most efficient delivery routes, reducing delivery times and costs.
Additionally, technologies like real-time package tracking can provide customers with visibility into the status of their orders, increasing satisfaction and reducing customer inquiries.
Efficient order fulfillment not only benefits the customers but also the businesses themselves. By reducing errors and speeding up the process, businesses can save costs associated with returns, replacements, and customer complaints.
Moreover, satisfied customers are more likely to become repeat customers and recommend the business to others, leading to increased sales and growth.
Traditional Methods of Order Fulfillment
Prior to the advent of technology, order fulfillment was primarily handled manually. This involved keeping track of inventory using pen and paper and manually processing orders. While this method may have sufficed for small businesses with a limited number of orders, it quickly became inefficient as sales volumes increased.
Let's dive deeper into the traditional methods of order fulfillment and explore the challenges businesses faced.
Manual Order Fulfillment
Manual order fulfillment relied heavily on human labor and was susceptible to human errors. Each step of the process, from taking orders to physically picking and packing items, was time-consuming and prone to mistakes.
Not only did this slow down the fulfillment process, but it also increased the chances of shipping incorrect items, resulting in dissatisfied customers and costly returns.
Imagine a small business owner, surrounded by stacks of paper, meticulously jotting down each order received. They would then have to cross-reference the inventory manually, searching through shelves and storage areas to find the requested items.
This process was not only labor-intensive but also left room for errors. Misreading an order or picking the wrong item from the shelves could lead to frustrated customers and potential loss of business.
Moreover, packing the items for shipment involved careful attention to detail. Each item had to be properly wrapped, labeled, and placed in the right package. Without technology to assist in this process, the chances of incorrect packaging or missing items were significantly higher.
Challenges with Traditional Order Fulfillment
In addition to human errors, traditional order fulfillment faced several challenges. Difficulty in tracking inventory accurately, limited visibility into the status of orders, and the lack of real-time communication were just a few of the obstacles businesses had to overcome.
These challenges not only affected operational efficiency but also hindered the ability to scale and meet growing customer demands.
Tracking inventory manually was a daunting task. Counting items, updating records, and ensuring accuracy required significant time and effort.
Businesses had to rely on physical counts, which were prone to errors and often led to discrepancies between recorded and actual inventory levels. This made it challenging to fulfill orders promptly and accurately.
Furthermore, without real-time visibility into the status of orders, businesses struggled to provide accurate information to customers regarding order processing and delivery timelines. Customers were left in the dark, unsure of when their orders would arrive. This lack of transparency often resulted in frustration and dissatisfaction.
Communication with customers was also a challenge. Traditional methods relied on phone calls or written correspondence, which were time-consuming and lacked efficiency.
Businesses had to manually update customers on order status and address any concerns or inquiries. This not only slowed down the entire process but also limited the ability to provide timely and satisfactory customer service.
In conclusion, while traditional methods of order fulfillment served their purpose in the past, they were riddled with challenges and limitations.
The need for a more efficient and accurate solution became evident as businesses grew and customer expectations evolved. The next section will explore how technology revolutionized the order fulfillment process and paved the way for more streamlined and effective operations.
As technology continues to advance, the possibilities for optimizing order fulfillment are endless. From improved inventory management to automated picking and packing, businesses can leverage technology to transform their operations and deliver exceptional customer experiences. Embracing these technological innovations will undoubtedly give businesses a competitive edge in today's rapidly evolving marketplace.
Looking for More Insights?
If you're keen on diving deeper into the intricacies of order management and ecommerce, these articles might be of interest:
- How to Calculate Fulfillment Cost Per Order
- How to Source Suppliers for Online Store
- How Does Herbalife Business Work
These posts will provide you with further insights into optimizing your ecommerce operations and understanding the logistics behind successful businesses.
FAQ
Related blogs
.avif)
Private Label Supplement Manufacturers: How To Find The Right Partner
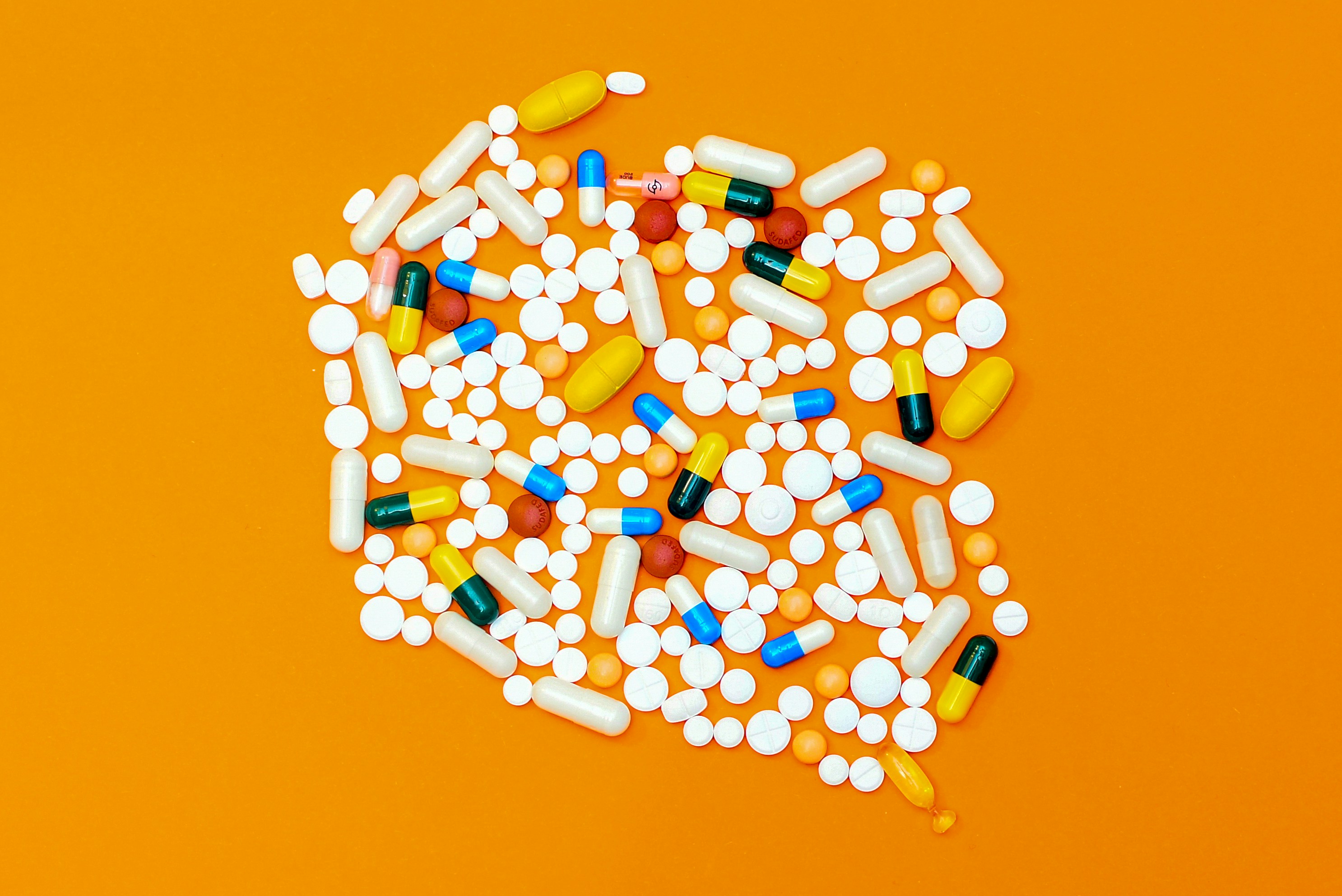
Private Label Supplements In Europe: How To Get Started
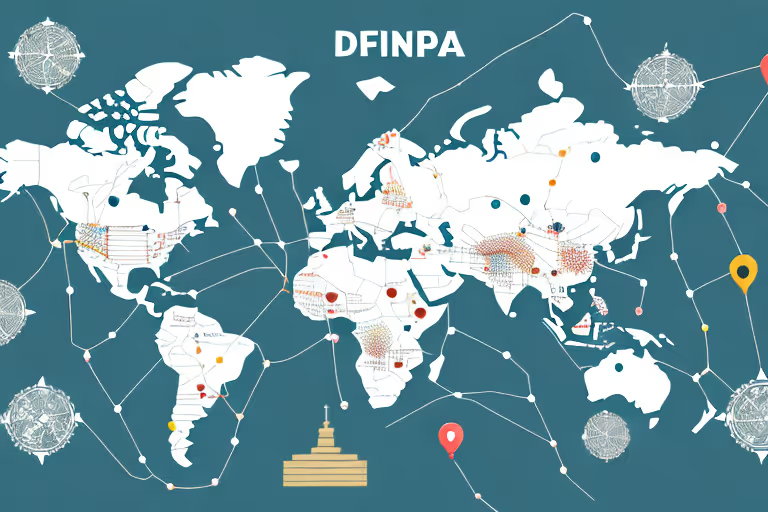