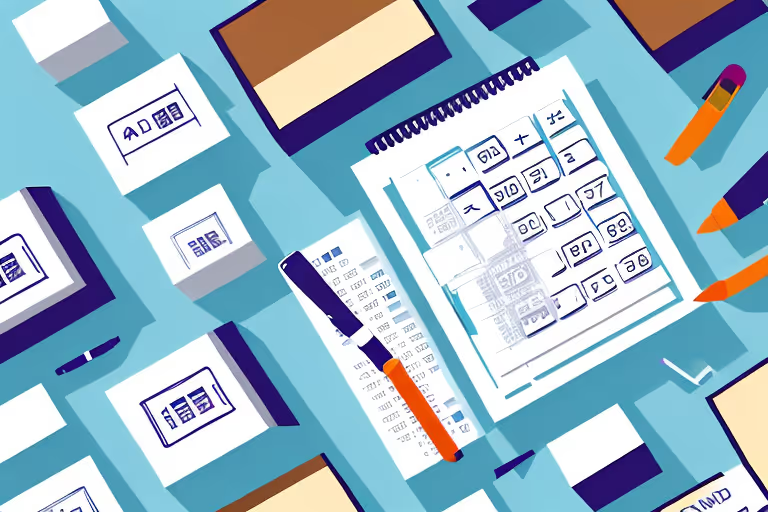
In this article, we will discuss the importance of fulfillment cost per order, its components, and provide a step-by-step guide on how to calculate it. We will also explore some useful tools and software that can assist you in this process.
Step-by-Step Guide to Calculate Fulfillment Cost Per Order
Now that we understand the importance of calculating fulfillment cost per order and its components, let's explore a step-by-step guide to help you calculate it accurately:
Step01: Gathering Necessary Data
The first step in calculating fulfillment cost per order is to gather all the relevant data. This includes information on warehousing costs, packaging and shipping costs, labor costs, returns processing costs, and any other direct or indirect expenses associated with fulfilling customer orders.
When gathering data on warehousing costs, it's important to consider factors such as rent or mortgage payments, property taxes, insurance, utilities, equipment maintenance, and any other costs directly related to storing and managing inventory.
By taking all these costs into account, you can accurately determine the true cost of warehousing.
Additionally, packaging and shipping costs should include expenses related to materials, such as boxes, tape, cushioning materials, labels, and any other supplies needed to package orders securely.
Shipping costs should account for carrier fees, fuel surcharges, customs duties, and any other charges associated with delivering orders to customers.
Labor costs are another crucial component to consider. This includes wages or salaries for fulfillment center staff, as well as any benefits or incentives provided to employees.
It's important to accurately track the time spent on fulfilling orders, including picking, packing, and shipping, as this will contribute to the overall fulfillment cost per order.
Lastly, returns processing costs should be factored in. This includes expenses related to inspecting returned items, restocking inventory, processing refunds or exchanges, and any associated shipping or packaging costs.
Returns processing can be a significant cost for businesses, so it's crucial to include it in the calculation of fulfillment cost per order.
Step02: Allocating Costs to Each Component
Once you have gathered all the necessary data, the next step is to allocate each cost to its respective component. For example, if you have data on warehouse rent, insurance, and utilities, you would allocate those costs to the warehousing component.
Similarly, packaging materials and shipping fees would be allocated to the packaging and shipping component.
Be sure to consider both direct costs, which can be easily attributed to a specific component, as well as indirect costs, which may require some estimation or allocation based on a predetermined formula or percentage.
For instance, if you have a fulfillment center that handles both warehousing and packaging, you may need to allocate a portion of the labor costs to each component based on the time spent on each activity.
This can be done by tracking the time spent on each task and using that information to determine the proportion of labor costs that should be allocated to each component.
Similarly, if you have shared resources, such as equipment or utilities, that are used for multiple components, you will need to allocate a portion of the costs to each component based on their usage.
This can be done by determining the percentage of usage for each component and applying that percentage to the total cost of the shared resource.
Step03: Calculating the Total Fulfillment Cost
After allocating costs to each component, you can calculate the total fulfillment cost per order by summing up all the costs. This will give you a comprehensive view of the expenses involved in fulfilling a single customer order.
It's important to update and review this calculation periodically, as costs may change over time. By keeping track of your fulfillment cost per order, you can identify trends and patterns, as well as make adjustments to your operations to maintain profitability.
Furthermore, analyzing the fulfillment cost per order can provide valuable insights into the efficiency of your fulfillment process. By comparing the cost per order over time or benchmarking it against industry standards, you can identify areas for improvement and implement strategies to reduce costs without compromising on quality or customer satisfaction.
In conclusion, calculating the fulfillment cost per order is a crucial step in understanding the financial implications of order fulfillment. By following this step-by-step guide and considering all the relevant components and costs, you can accurately determine the true cost of fulfilling customer orders and make informed decisions to optimize your operations.
Tools and Software for Calculating Fulfillment Cost
Calculating fulfillment cost per order can be a complex task, especially for businesses with numerous orders and components. Fortunately, there are several tools and software available that can simplify the process and provide accurate calculations. Let's explore some of these tools:
1. Inventory Management Systems
Inventory management systems, such as ABC Inventory or Fishbowl, can help businesses track and manage their inventory. These systems often include features that allow users to input various costs associated with inventory management, including warehousing costs, labor costs, and returns processing costs.
With accurate data input, these systems can provide valuable insights into the fulfillment cost per order.
2. Order Management Systems
Order management systems, like Orderhive or TradeGecko, enable businesses to seamlessly manage their orders from placement to fulfillment. These systems can integrate with other systems, such as inventory management or shipping management systems, to provide a comprehensive view of the fulfillment process.
Some order management systems also include cost tracking features that can assist in calculating fulfillment cost per order.
3. Shipping and Delivery Management Systems
Shipping and delivery management systems, such as ShipStation or Shippo, help businesses streamline their shipping processes. These systems often have features that track shipping costs and allow businesses to compare rates from different carriers.
By using these systems, businesses can accurately calculate the packaging and shipping costs component of the fulfillment cost per order.
Understanding Fulfillment Cost Per Order
To grasp the concept of fulfillment cost per order, let's start with a brief definition. Fulfillment cost per order refers to the total expenses a business incurs to fulfill a single customer order from start to finish.
This cost includes various factors like warehousing, packaging and shipping, labor, and returns processing, among others. By calculating the fulfillment cost per order accurately, businesses can gain valuable insights into their operations and identify opportunities to reduce expenses while maintaining customer satisfaction.
What is Fulfillment Cost Per Order?
Fulfillment cost per order encompasses all the expenses associated with fulfilling a customer order. These expenses include not only direct costs related to warehousing, packaging, shipping, and labor, but also indirect costs such as overheads and administrative expenses.
By considering both direct and indirect costs, businesses can have a comprehensive understanding of the true cost of fulfilling an order.
Let's delve deeper into the direct costs involved in fulfillment.
- Warehousing costs cover the expenses of storing inventory, including rent, utilities, and equipment.
- Packaging and shipping costs include materials like boxes, tape, and labels, as well as the actual shipping fees charged by carriers.
- Labor costs encompass the wages or salaries of employees involved in the fulfillment process, such as pickers, packers, and shipping personnel.
On the other hand, indirect costs play a crucial role in determining the overall fulfillment cost per order. Overheads, which include expenses like rent for office space, utilities, and insurance, contribute to the indirect costs.
Administrative expenses, such as salaries of management and support staff, as well as software and technology costs, also factor into the fulfillment cost per order.
Calculating fulfillment cost per order is crucial for several reasons. Firstly, it helps businesses understand the profitability of individual orders and product lines.
By analyzing the fulfillment cost per order alongside revenue generated, businesses can identify which products or orders are the most profitable and which ones may be costing more than they bring in.
Moreover, calculating fulfillment cost per order allows businesses to identify areas for improvement and cost reduction. By conducting a thorough analysis, businesses can pinpoint the major cost drivers and implement strategies to optimize their operations.
For example, they may identify that certain products require excessive packaging materials, leading to higher costs. By finding alternative packaging solutions, businesses can reduce expenses without compromising product safety or presentation.
In addition to cost reduction, calculating fulfillment cost per order also aids in pricing decisions. By accurately estimating the costs associated with fulfilling an order, businesses can set prices that are both competitive and profitable.
This ensures that the business remains sustainable in the long run and can continue to provide high-quality products and services to customers.
Furthermore, understanding the fulfillment cost per order allows businesses to evaluate the efficiency of their fulfillment processes. By analyzing the time and resources required to fulfill an order, businesses can identify bottlenecks and areas where improvements can be made.
For instance, they may discover that certain products require excessive handling or have complex packaging requirements, leading to delays in the fulfillment process. By streamlining these processes, businesses can improve overall efficiency and customer satisfaction.
In conclusion, calculating fulfillment cost per order provides businesses with valuable insights into their operations, profitability, and areas for improvement. By considering both direct and indirect costs, businesses can accurately estimate the true cost of fulfilling an order.
This knowledge empowers businesses to make informed decisions, optimize their operations, and ultimately enhance customer satisfaction while maintaining profitability.
Components of Fulfillment Cost Per Order
The fulfillment cost per order consists of several key components. Let's take a closer look at each of them and understand their significance in the overall calculation:
1. Warehousing Costs
Warehousing costs include expenses associated with storing and managing inventory. This may include rent or mortgage payments, utilities, insurance, and equipment costs. By accurately tracking warehousing costs, businesses can evaluate the efficiency of their storage operations and make informed decisions regarding inventory management.
Furthermore, warehousing costs can also encompass additional expenses such as security measures to protect valuable inventory from theft or damage. This may include investing in surveillance systems, hiring security personnel, or implementing access control measures to ensure the safety and integrity of stored goods.
Moreover, businesses may also need to consider the costs of implementing inventory management software or systems to streamline their warehousing operations. These tools can help automate processes such as inventory tracking, order fulfillment, and stock replenishment, ultimately reducing errors and improving overall efficiency.
2. Packaging and Shipping Costs
Packaging and shipping costs are incurred when preparing the product for shipment and delivering it to the customer. This includes materials like boxes, bubble wrap, and tape, as well as shipping fees, postage, and any additional handling charges.
Analyzing packaging and shipping costs can help businesses identify cost-saving opportunities, such as negotiating better rates with shipping carriers or using more cost-effective packaging materials.
In addition to the direct costs of packaging materials and shipping fees, businesses must also consider indirect costs associated with packaging and shipping.
For example, investing in packaging materials that provide better protection for fragile items can help reduce the number of damaged goods and subsequent returns, saving both time and money.
Furthermore, businesses may also need to factor in the costs of implementing shipping software or systems that can automate processes such as label printing, tracking, and order fulfillment. These tools can help streamline the shipping process, reduce errors, and improve customer satisfaction.
3. Labor Costs
Labor costs make up a significant portion of the fulfillment cost per order. This includes wages, benefits, and other expenses related to the employees involved in the fulfillment process, such as pickers, packers, and shipping personnel.
By understanding labor costs, businesses can assess the productivity and efficiency of their fulfillment team and identify opportunities for process improvement.
When considering labor costs, businesses should also take into account the training and development expenses associated with maintaining a skilled and efficient fulfillment team. Investing in employee training programs or certifications can enhance the team's capabilities, leading to improved productivity and reduced fulfillment errors.
Moreover, businesses may also need to consider the costs of employee benefits such as health insurance, retirement plans, and paid time off. These benefits are essential for attracting and retaining talented employees in a competitive job market.
4. Returns Processing Costs
Returns processing costs refer to the expenses associated with handling and processing returned items from customers. These costs may include restocking fees, labor costs for inspecting and re-stocking returned items, and any additional costs related to refurbishing or disposing of returned products.
Tracking returns processing costs can help businesses evaluate the effectiveness of their return management processes and streamline operations to minimize returns and associated expenses.
In addition to the direct costs of processing returns, businesses should also consider the indirect costs associated with returns. For example, the negative impact on customer satisfaction and potential damage to the brand's reputation can have long-term consequences.
Investing in efficient return management processes and systems can help reduce the number of returns, improve customer experience, and mitigate these indirect costs.
Furthermore, businesses may also need to allocate resources for customer service representatives who handle return inquiries and provide support to customers throughout the returns process. These representatives play a crucial role in ensuring customer satisfaction and resolving issues promptly and efficiently.
In conclusion, calculating the fulfillment cost per order is a crucial task for businesses looking to optimize their operations and maximize profits. By understanding the components that make up this cost and following a step-by-step guide, businesses can accurately calculate their fulfillment cost per order and identify opportunities for improvement.
Additionally, utilizing tools and software specifically designed for this purpose can simplify and automate the calculation process. With this knowledge and the right tools at hand, businesses can make informed decisions to reduce expenses, increase profitability, and ultimately provide a better experience for their customers.
Seeking More Insights into E-commerce Logistics?
If you're diving into the complexities of e-commerce operations, these articles will be your guide:
https://supliful.com/blog/how-do-returns-work-with-dropshipping
https://supliful.com/blog/can-you-advertise-supplements-on-facebook
https://supliful.com/blog/how-to-use-reddit-to-promote-youtube-channel
Engage with these resources to further refine your e-commerce strategies and ensure a seamless experience for your customers.
FAQ
Related blogs
.avif)
Private Label Supplement Manufacturers: How To Find The Right Partner
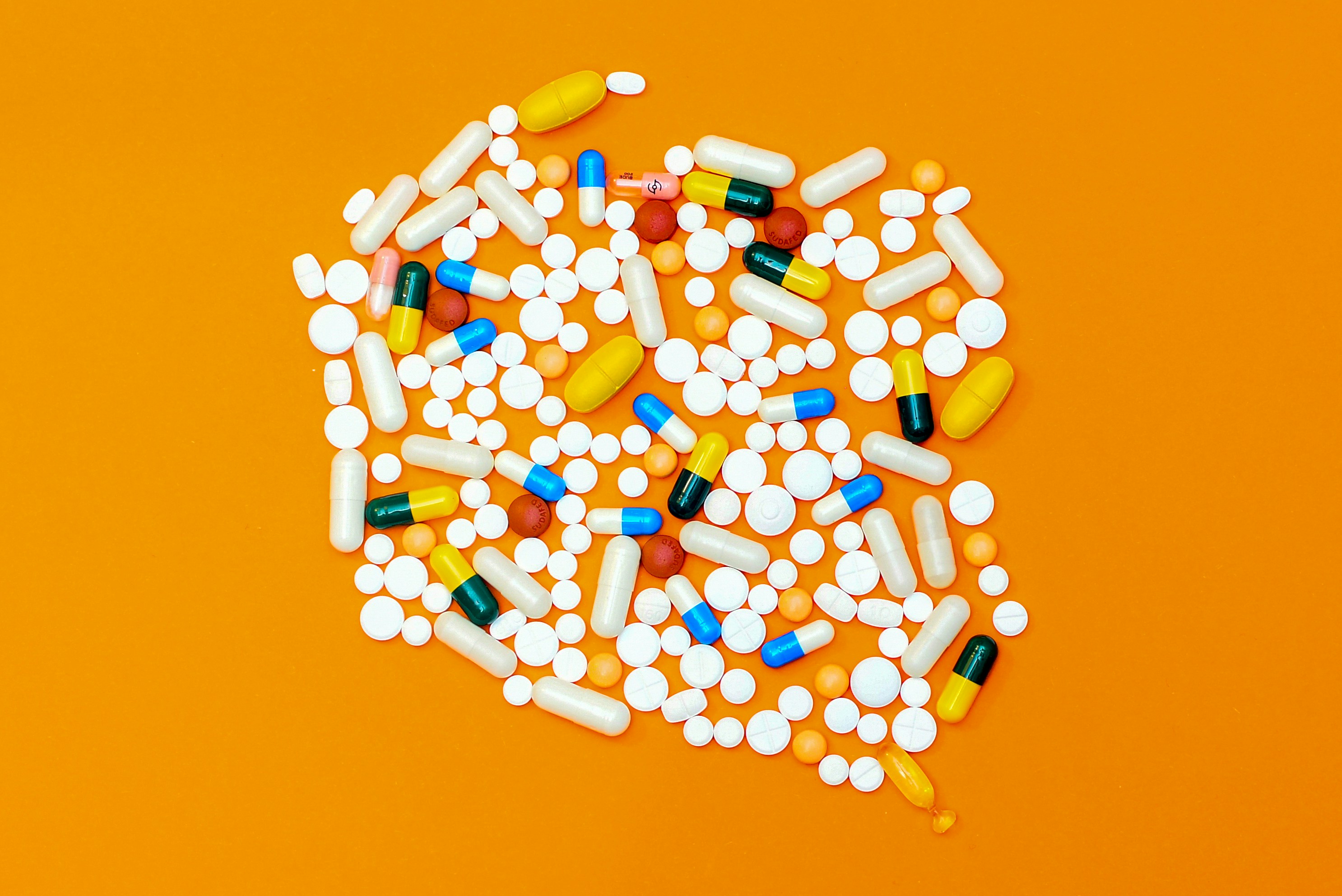
Private Label Supplements In Europe: How To Get Started
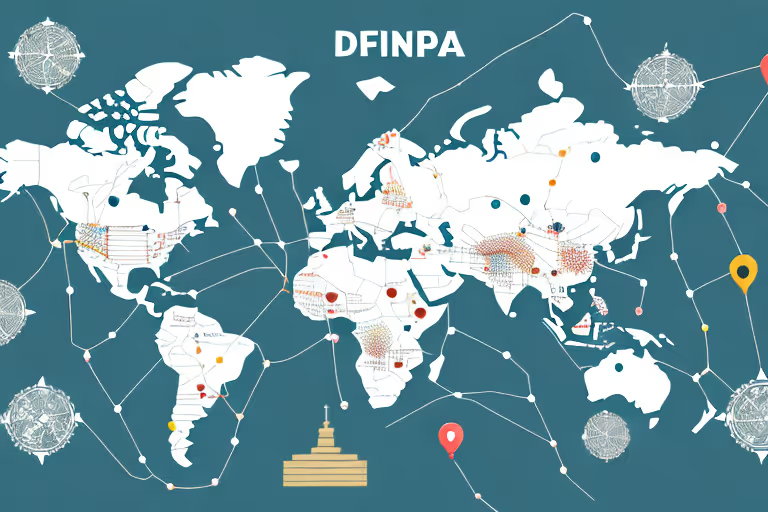