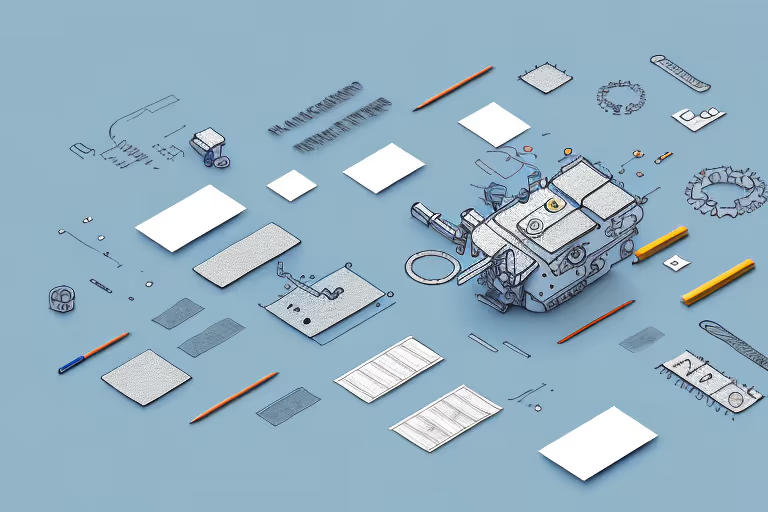
In this article, we will explore the definition of kitting, its significance in the manufacturing industry, the process involved, and the numerous benefits it offers. We will also delve into the challenges manufacturers may face when implementing kitting and provide effective solutions to overcome them.
Definition of Kitting in Manufacturing
Kitting, in the manufacturing context, refers to the process of gathering and organizing all the necessary components, parts, and materials required for a specific operation or project. These components are then packaged together as a kit, which is ready for use in the production process.
When it comes to kitting, precision and attention to detail are key. Each kit must be carefully assembled to ensure that all the required components are included and that they are in the correct quantities. This ensures that the production process can run smoothly without any interruptions or delays.
Kitting can be compared to preparing a recipe for cooking. Just as a chef gathers all the ingredients before starting to cook, manufacturers gather all the necessary components and materials before starting the production process. This allows for a more efficient and streamlined manufacturing operation.
The Importance of Kitting in the Manufacturing Process
Kitting plays a crucial role in streamlining manufacturing operations by reducing production time and enhancing overall efficiency. By organizing all the necessary components in advance, kitting eliminates the need for workers to search for individual parts, reducing the chances of errors, delays, and disruptions.
Imagine a scenario where workers have to search for each component separately, wasting precious time and effort. This not only slows down the production process but also increases the risk of mistakes.
With kitting, all the components are readily available, allowing workers to focus on the task at hand and ensuring a more efficient workflow.
Moreover, kitting helps improve inventory management by providing a clear and accurate overview of the components and materials required for each project. This allows manufacturers to optimize stock levels, reduce wastage, and ensure timely availability of necessary supplies.
By having a clear understanding of the components needed for each project, manufacturers can avoid overstocking or understocking.
Overstocking can lead to increased storage costs and the risk of materials becoming obsolete, while understocking can cause production delays and missed deadlines. Kitting helps strike the right balance, ensuring that the required components are always available without excessive inventory costs.
Furthermore, kitting enhances the overall organization and cleanliness of the manufacturing facility. With all the components neatly packaged and labeled, it becomes easier to maintain a clean and orderly workspace. This not only improves safety but also contributes to a positive work environment.
In conclusion, kitting is an essential process in manufacturing that involves gathering and organizing all the necessary components, parts, and materials for a specific operation or project.
By streamlining the production process, improving inventory management, and enhancing overall efficiency, kitting plays a vital role in ensuring smooth and successful manufacturing operations.
The Role of Kitting in Streamlining Operations
Kitting is a highly effective strategy used by manufacturers to streamline their operations and optimize efficiency. By pre-assembling all the required components into kits, manufacturers can eliminate the time-consuming process of searching for and gathering individual parts.
One of the primary benefits of kitting is its ability to significantly reduce production time. With all the necessary components readily available in the kits, workers can focus solely on the assembly process, rather than wasting valuable time searching for specific parts.
This streamlined approach not only speeds up the production process but also minimizes the risk of errors, as workers can concentrate on the task at hand.
Moreover, kitting allows for parallel processing, where multiple kits can be prepared simultaneously. This further boosts productivity and ensures a smooth and efficient workflow. With parallel processing, manufacturers can maximize their output without compromising on quality, leading to increased customer satisfaction.
How Kitting Reduces Production Time
Kitting is a game-changer when it comes to reducing production time. By organizing all the necessary components into kits, manufacturers can eliminate the need for workers to spend valuable time searching for individual parts. This not only saves time but also minimizes the risk of delays and disruptions in the production process.
Imagine a scenario where workers have to search through multiple bins and shelves to find specific parts. This can be a time-consuming and frustrating process, leading to unnecessary delays and decreased productivity.
However, with kitting, all the required components are conveniently grouped together, ready to be used. This allows workers to focus solely on the assembly process, resulting in a significant reduction in production time.
Furthermore, kitting enables manufacturers to implement efficient assembly line processes. By organizing the kits in a logical and systematic manner, manufacturers can ensure smooth and uninterrupted workflow. This eliminates any bottlenecks or inefficiencies in the production line, leading to improved overall productivity and faster turnaround times.
Kitting and Inventory Management: A Close Connection
Effective inventory management is crucial for manufacturers to avoid stockouts, reduce carrying costs, and ensure seamless production processes. Kitting plays a significant role in optimizing inventory management by providing a systematic approach to material handling and control.
By organizing components into kits, manufacturers can accurately track inventory levels and ensure timely replenishment. This eliminates the risk of stockouts, prevents production delays, and enables manufacturers to meet customer demands more efficiently.
With kitting, manufacturers have a clear overview of the components available and can plan their inventory replenishment accordingly.
Moreover, kitting allows for better control and visibility over the inventory. By having components organized and grouped into kits, manufacturers can easily identify excess stock or shortages. This helps in reducing the chances of overstocking or understocking, leading to improved cost efficiency and better utilization of resources.
Additionally, kitting facilitates the implementation of just-in-time (JIT) inventory management strategies. With JIT, manufacturers can minimize inventory holding costs, reduce the risk of obsolete inventory, and improve cash flow.
By having kits readily available, manufacturers can ensure that the right components are delivered at the right time, avoiding unnecessary inventory buildup.
In conclusion, kitting is a valuable tool for manufacturers looking to streamline their operations and optimize efficiency. By pre-assembling components into kits, manufacturers can reduce production time, improve inventory management, and enhance overall productivity.
With its numerous benefits, kitting has become an essential strategy for manufacturers seeking to stay competitive in today's fast-paced and demanding market.
The Process of Kitting in Manufacturing
Kitting is an essential process in manufacturing that involves the efficient gathering, organizing, and packaging of components and materials required for a specific project or operation. This process ensures that all the necessary items are conveniently grouped together, ready for use in the production process. Let's take a closer look at the step-by-step guide to the kitting process.
Step-by-Step Guide to the Kitting Process
The kitting process typically involves the following steps:
- Planning: Before starting the kitting process, it is crucial to identify the components and materials required for a specific project or operation. This involves analyzing the production requirements and determining the exact quantities of each item needed.
- Gathering: Once the planning phase is complete, the next step is to collect all the necessary components and materials from the inventory. This may involve retrieving items from different locations within the facility or even sourcing them from external suppliers.
- Organizing: After gathering all the required components, it is essential to arrange them in a structured and systematic manner. This can be done using storage bins or containers, which provide a designated space for each item, ensuring easy accessibility and efficient organization.
- Kit Assembly: Once the components are organized, the next step is to package them together as a kit. This involves carefully placing each item in the designated container or packaging material, ensuring that they are secure and protected during transportation and storage.
- Labeling: To avoid confusion and facilitate easy identification, it is crucial to clearly label each kit with relevant information. This may include part numbers, quantities, serial numbers, or any other necessary details. Labels and labeling equipment play a vital role in ensuring accurate identification and tracking of the kits.
- Storage: Finally, the assembled kits are stored in a designated area, ready for use in the production process. Proper storage is essential to maintain the integrity of the kits and prevent any damage or misplacement. This may involve using shelves, racks, or other storage systems to keep the kits organized and easily accessible.
Essential Tools and Equipment for Kitting
To effectively carry out the kitting process, manufacturers require various tools and equipment. These include:
- Storage Bins or Containers: Provide a designated space for organizing and storing the kit components. These bins or containers come in various sizes and shapes, allowing for efficient organization and easy access to the items.
- Labels and Labeling Equipment: Ensure clear and accurate identification of the kits. Labels can be customized with relevant information, such as part numbers, descriptions, or barcodes. Labeling equipment, such as printers or label makers, streamline the labeling process and ensure consistency.
- Inventory Management Software: Facilitate efficient tracking and control of kits and their corresponding components. This software allows manufacturers to monitor inventory levels, track the movement of kits, and generate reports for better inventory management.
- Material Handling Equipment: Aid in the movement and transportation of components during the kitting process. This includes equipment such as forklifts, pallet jacks, or conveyors, which help streamline the process and reduce the risk of damage or injuries.
By utilizing these tools and following the step-by-step guide to the kitting process, manufacturers can ensure a smooth and efficient production workflow. Kitting plays a crucial role in optimizing inventory management, reducing assembly time, and improving overall productivity in the manufacturing industry.
Benefits of Implementing Kitting in Manufacturing
Cost Efficiency through Kitting
Kitting offers numerous cost-saving benefits for manufacturers. By reducing production time, minimizing the risk of errors, and optimizing inventory management, kitting enables manufacturers to enhance overall operational efficiency.
This, in turn, leads to significant cost savings, as manufacturers can produce more in less time while eliminating unnecessary expenses related to excess inventory or production delays.
Improving Product Quality with Kitting
Kitting plays a crucial role in maintaining product quality and consistency. By ensuring that all the necessary components are readily available in the correct quantities, kitting minimizes the risk of using incorrect or faulty parts. This enhances the overall quality of the final product, resulting in improved customer satisfaction and loyalty.
Challenges and Solutions in Kitting
Common Obstacles in Implementing Kitting
While kitting offers numerous benefits, manufacturers may encounter certain challenges during its implementation. These challenges include:
- Complicated Supply Chain: Manufacturers may face difficulties in coordinating with suppliers to ensure timely availability of components and materials. Streamlining the supply chain and establishing effective communication channels can help address this challenge.
- Inventory Management Complexity: Managing inventory levels and avoiding stockouts can be a complex task. Implementing robust inventory management systems and utilizing real-time data can help overcome this challenge.
- Resistance to Change: Introducing new processes and systems can face resistance from employees. Proper training, communication, and involvement of the workforce can help mitigate this challenge.
Effective Solutions for Kitting Challenges
To overcome the challenges associated with kitting, manufacturers can consider implementing the following solutions:
- Collaborative Supplier Relationships: Foster strong relationships with suppliers to ensure timely and reliable delivery of components and materials.
- Integration of Technology: Utilize inventory management software and real-time data analysis to streamline inventory control and enhance supply chain visibility.
- Employee Training and Engagement: Provide comprehensive training and involve employees in the implementation process to gain their buy-in and minimize resistance to change.
For instance, imagine a scenario where workers have to search through multiple bins and shelves to find specific parts. This can be a time-consuming and frustrating process, leading to unnecessary delays and decreased productivity. However, with kitting, all the required components are conveniently grouped together, ready to be used. This allows workers to focus solely on the assembly process, resulting in a significant reduction in production time. If you're keen on understanding more about inventory management and supplier negotiations, learning how to negotiate a lower MOQ can be beneficial.
In conclusion, kitting plays a vital role in the manufacturing industry, offering numerous benefits such as reduced production time, improved inventory management, cost efficiency, and enhanced product quality. However, implementing kitting may involve certain challenges, which can be overcome through collaborative supplier relationships, technology integration, and effective employee training. By embracing kitting and optimizing its implementation, manufacturers can achieve greater operational efficiency and stay ahead in the competitive manufacturing landscape.
Dive Deeper into Manufacturing Insights
If you're interested in further exploring the nuances of manufacturing and inventory management, the following articles are a must-read:
- How to Fulfill Orders on Shopify Dropshipping
- How E-commerce Warehouse Works
- How to Automate a Shopify Store
These pieces delve into the intricacies of managing inventory, optimizing manufacturing processes, and leveraging technology for e-commerce success.
FAQ
Related blogs
.avif)
Private Label Supplement Manufacturers: How To Find The Right Partner
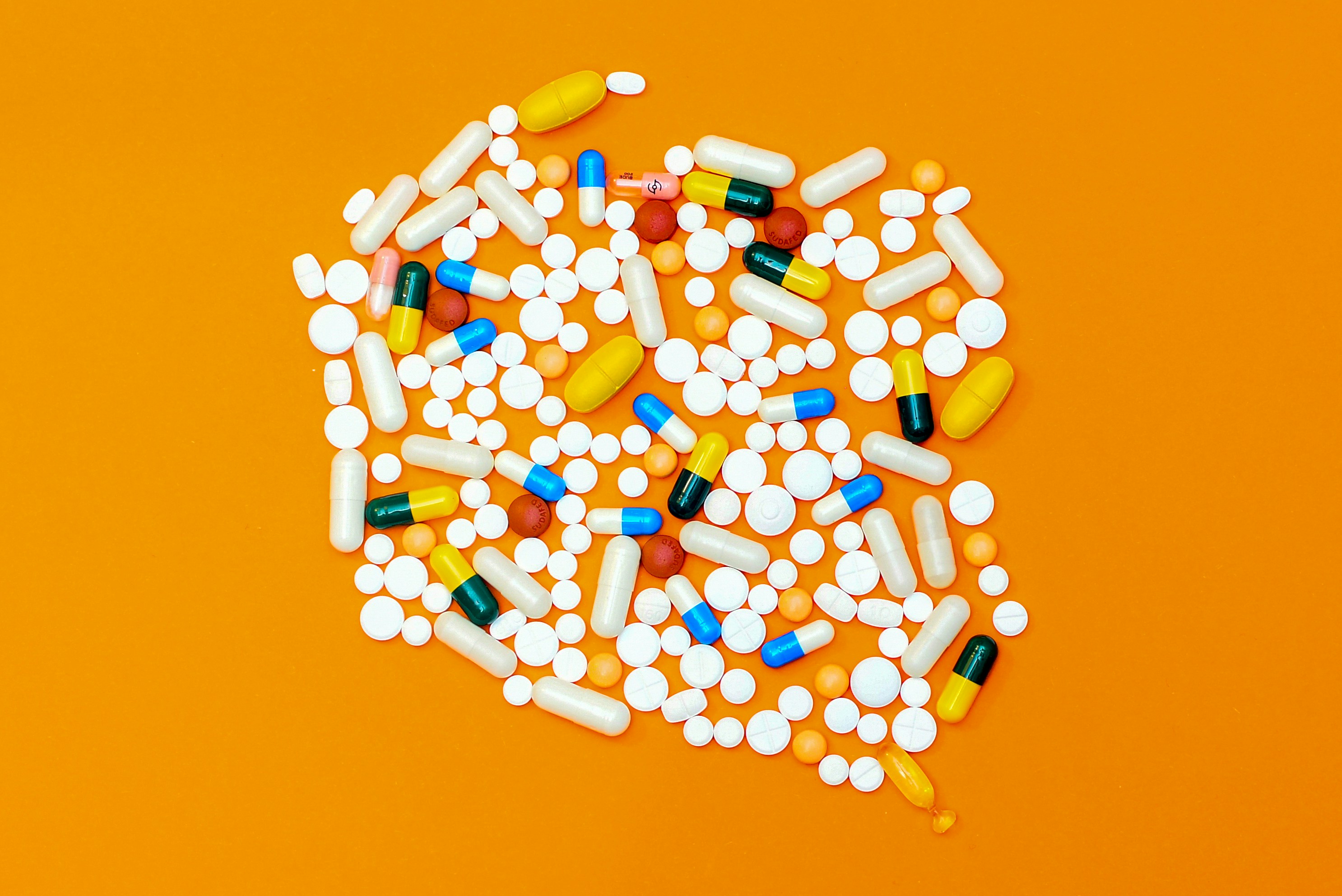
Private Label Supplements In Europe: How To Get Started
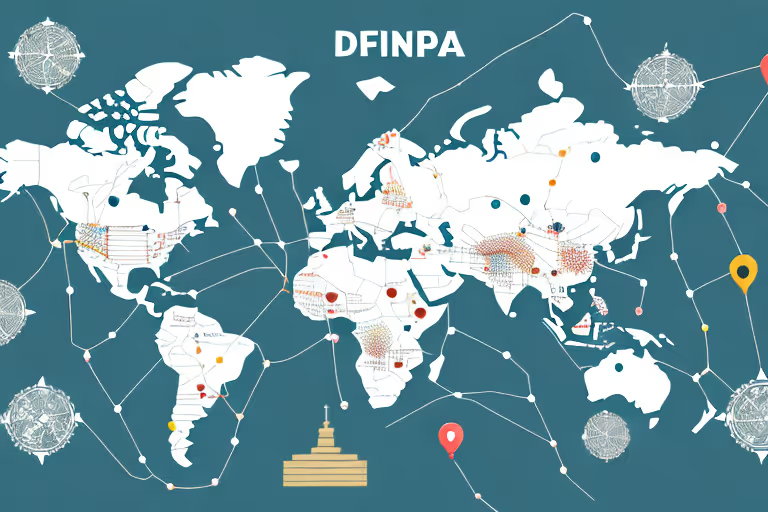