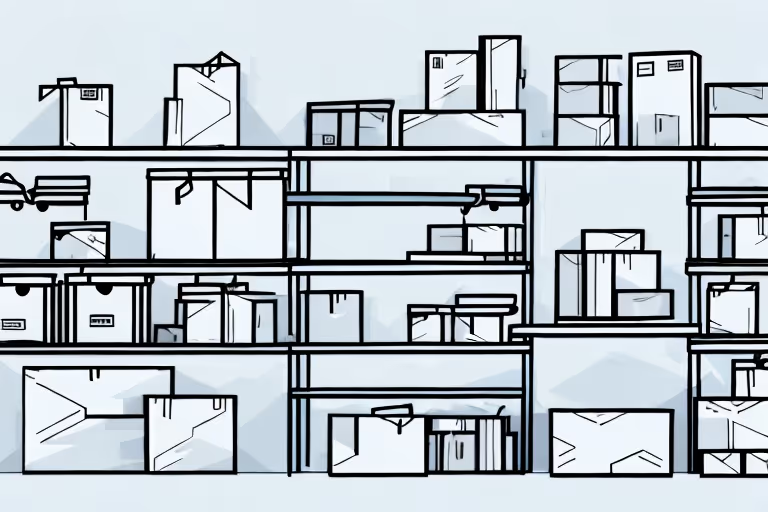
To truly grasp the inner workings of this vital component of the e-commerce industry, let's delve into the basics of e-commerce warehousing and explore its various facets.
Understanding E-Commerce Warehousing: How It Functions
In the fast-paced world of e-commerce, a well-functioning warehouse plays a pivotal role in ensuring seamless order fulfillment and customer satisfaction. From receiving and organizing inventory to shipping out packages, an e-commerce warehouse is the heart of the entire operation.
In this blog, we will take you on a detailed journey into how an e-commerce warehouse works, providing a comprehensive understanding of the processes involved.
1. Receiving and Inventory Management:
The first step in the e-commerce warehouse process is receiving products from suppliers. Upon arrival, warehouse staff thoroughly inspect the incoming shipments to ensure the items are in good condition and match the order details.
Next, the inventory is carefully organized and assigned designated locations within the warehouse. Modern e-commerce warehouses often employ inventory management systems to track stock levels, monitor product movement, and automate reorder processes.
2. Order Processing:
When a customer places an order through the e-commerce platform, the warehouse receives the order details electronically. This triggers the order processing stage, where warehouse staff pick the required items from the inventory shelves.
The items are then verified against the order to ensure accuracy before moving on to the packing stage.
3. Packing and Labeling:
The packing stage involves carefully packing the ordered items in appropriate packaging materials, taking care to protect delicate or fragile items. E-commerce warehouses typically use packaging solutions tailored to the specific needs of different products.
Once packed, the packages are labeled with shipping details, including the destination address and tracking information. Proper labeling is crucial for smooth and efficient logistics.
4. Shipping and Logistics:
With packages fully prepared, the e-commerce warehouse hands them over to shipping carriers for delivery. The chosen carrier transports the packages to their respective destinations based on the shipping method selected by the customer during checkout.
Many e-commerce platforms integrate directly with shipping carriers, enabling real-time tracking and automatic updates for customers.
5. Returns and Exchanges:
E-commerce warehouses handle customer returns and exchanges as part of their order fulfillment process. Returned items are carefully inspected to determine their condition. If the returned items are in a sellable condition, they are returned to inventory.
If the items are damaged or not fit for resale, appropriate actions are taken, such as restocking or disposal.
6. Inventory Replenishment:
As products are sold, the e-commerce warehouse continuously monitors inventory levels. When stock levels reach a certain threshold, the warehouse initiates a replenishment process to restock popular items and ensure a sufficient supply. Inventory management systems play a crucial role in maintaining a well-balanced stock level.
7. Technology and Automation:
Many e-commerce warehouses leverage technology and automation to streamline processes, increase efficiency, and reduce errors. Barcode scanning, automated conveyor belts, and robot-assisted order picking are some examples of how technology enhances warehouse operations.
Automation not only speeds up the order fulfillment process but also ensures accuracy in inventory tracking and reduces the chances of human error.
Behind the smooth online shopping experience lies a sophisticated and well-organized e-commerce warehouse. From receiving products to shipping them to customers, the e-commerce warehouse works tirelessly to fulfill orders efficiently and meet customer expectations.
By understanding how e-commerce warehouses operate, businesses can optimize their order fulfillment process, improve customer satisfaction, and drive success in the competitive world of e-commerce.
The Structure of an E-Commerce Warehouse
The physical layout and design of an e-commerce warehouse play a pivotal role in its efficiency and productivity. Let's explore two key aspects that contribute to the overall effectiveness of these warehouses: layout and design, as well as inventory management systems.
Layout and Design
Efficient warehouse layout and design are essential for maximizing storage capacity and ensuring smooth operations. When it comes to the layout, warehouses often adopt different strategies based on their specific needs.
One common layout is the "cross-docking" approach, where incoming products are immediately transferred to outbound vehicles, minimizing the need for storage. This layout is particularly beneficial for e-commerce warehouses that prioritize fast order fulfillment and have a high turnover of goods.
Another layout strategy is the "zone picking" method, where the warehouse is divided into different zones dedicated to specific product categories. This allows for streamlined picking and packing processes, as workers can focus on a specific area and become experts in handling those particular products.
Additionally, the use of conveyor belts and automated sorting systems can further optimize the layout, reducing the time and effort required to move products from one area to another.
Furthermore, the design of an e-commerce warehouse involves considerations such as the height of the storage racks, the width of the aisles, and the placement of equipment and machinery.
By utilizing vertical space effectively, warehouses can increase their storage capacity without expanding the physical footprint. Narrow aisles and the use of forklifts or automated guided vehicles (AGVs) can also enhance efficiency by allowing for quick and precise movement of goods.
Inventory Management Systems
Accurate inventory management is crucial in e-commerce warehousing. To effectively track and manage inventory, advanced inventory management systems are employed.
These systems use technologies such as barcodes and radio frequency identification (RFID) to monitor stock levels, locate products within the warehouse, and provide real-time updates on inventory availability.
In addition to barcodes and RFID, some warehouses also utilize automated storage and retrieval systems (AS/RS) to further enhance their inventory management capabilities.
AS/RS systems use robotic arms or cranes to retrieve and store products, eliminating the need for manual labor and reducing the risk of errors. These systems can handle large volumes of inventory with high precision and speed, ensuring accurate order fulfillment and minimizing the chances of stockouts.
Moreover, e-commerce warehouses often integrate their inventory management systems with their online platforms and order processing systems.
This integration allows for seamless synchronization of inventory data, ensuring that customers can only place orders for products that are actually in stock. It also enables real-time inventory updates, preventing overselling and improving customer satisfaction.
By having a precise understanding of inventory levels, e-commerce warehouses can avoid stockouts and ensure timely order fulfillment. This not only improves customer satisfaction but also reduces the costs associated with stock shortages and excess inventory.
The Role of Technology in E-Commerce Warehouses
With the rapid advancements in technology, e-commerce warehouses are leveraging various tech-driven solutions to optimize their operations. These technological advancements have revolutionized the industry, enabling warehouses to meet the increasing demands of online shopping.
Two notable technologies that have played a significant role in this transformation are Warehouse Management Systems (WMS) and robotics and automation.
Warehouse Management Systems (WMS)
Warehouse Management Systems (WMS) are software applications that enable efficient warehouse operations by automating various tasks. These systems help manage inventory levels, track order progress, and allocate resources effectively.
By integrating WMS into their operations, e-commerce warehouses can streamline workflows, reduce errors, and enhance overall productivity.
WMS provides real-time visibility into inventory levels, allowing warehouses to accurately track stock levels and prevent stockouts. This ensures that customers can always find the products they need and receive their orders promptly.
Additionally, WMS enables warehouses to optimize storage space by suggesting the most efficient placement of products based on demand and accessibility. This not only maximizes warehouse capacity but also minimizes the time taken to locate and retrieve items.
Furthermore, WMS automates order fulfillment processes, reducing the likelihood of errors and improving order accuracy. By automating tasks such as order picking and packing, warehouses can minimize human intervention, which in turn reduces the chances of mistakes.
This not only improves customer satisfaction but also saves time and resources that would otherwise be spent on rectifying errors.
Robotics and Automation in Warehousing
Robots and automation technologies are transforming the e-commerce warehousing landscape. These advancements have brought about a significant shift in how warehouses operate, enabling them to keep up with the ever-increasing volume of online orders.
One of the key areas where robotics and automation have made a significant impact is in the picking and packing process. Automated picking systems use robotic arms equipped with sensors and cameras to identify and retrieve items from shelves.
These systems can work alongside human workers, increasing picking speed and accuracy. By automating this labor-intensive task, e-commerce warehouses can significantly reduce the time it takes to fulfill orders, ensuring faster delivery to customers.
In addition to automated picking systems, robotic-guided vehicles (RGVs) are increasingly being used for transporting goods within warehouses. These autonomous vehicles can navigate through the warehouse, following predefined routes or using advanced mapping technology.
RGVs can transport goods between different areas of the warehouse, reducing the need for manual labor and increasing operational efficiency.
Furthermore, automation technologies such as conveyor systems and sorting machines have streamlined the order fulfillment process. These systems can handle large volumes of orders, sorting and routing items to the appropriate destinations with speed and accuracy.
By automating these tasks, e-commerce warehouses can handle a higher volume of orders, improving overall productivity.
Overall, the integration of robotics and automation technologies in e-commerce warehouses has revolutionized the industry. These advancements have not only improved operational efficiency but also enhanced the customer experience by ensuring faster order fulfillment and accurate inventory management.
As technology continues to advance, e-commerce warehouses will undoubtedly continue to embrace new solutions to further optimize their operations and meet the evolving demands of online shoppers.
Challenges in E-Commerce Warehousing
While e-commerce warehousing plays a critical role in the success of online retail, it also faces various challenges. Let's take a closer look at two key challenges these warehouses encounter: managing high volume orders and handling returns and exchanges.
Managing High Volume Orders
The ever-increasing popularity of online shopping brings immense pressure on e-commerce warehouses to handle high volume orders efficiently. The warehouses must prioritize order processing accuracy and timely fulfillment without compromising on quality.
Investing in advanced technologies, optimizing warehouse layout, and employing efficient manpower are essential for meeting the demands of a growing customer base.
Dealing with Returns and Exchanges
Returns and exchanges are an inevitable part of the e-commerce industry. E-commerce warehouses must have robust return management processes in place to handle returned products effectively.
This involves inspecting returned items, updating inventory records, and processing refunds or exchanges. By efficiently managing returns, e-commerce warehouses can maintain customer satisfaction and minimize operational costs.
Understanding how e-commerce warehouses work is essential for both customers and online retailers. By appreciating the intricacies of these warehousing operations, customers can gain insight into the processes involved in delivering their online purchases. Online retailers, on the other hand, can leverage this knowledge to optimize their supply chain, enhance customer experiences, and achieve long-term success in the e-commerce industry.
Looking for More Wisdom?
If you're keen to dive deeper into the world of e-commerce and warehousing, these articles might be of interest:
- How Long Does It Take to Make Money on Shopify?
- How to Automate a Shopify Store
- How to Fulfill Orders on Shopify Dropshipping
These posts will provide further insights into optimizing your e-commerce operations and understanding the intricacies of warehousing.
FAQ
Related blogs
.avif)
Private Label Supplement Manufacturers: How To Find The Right Partner
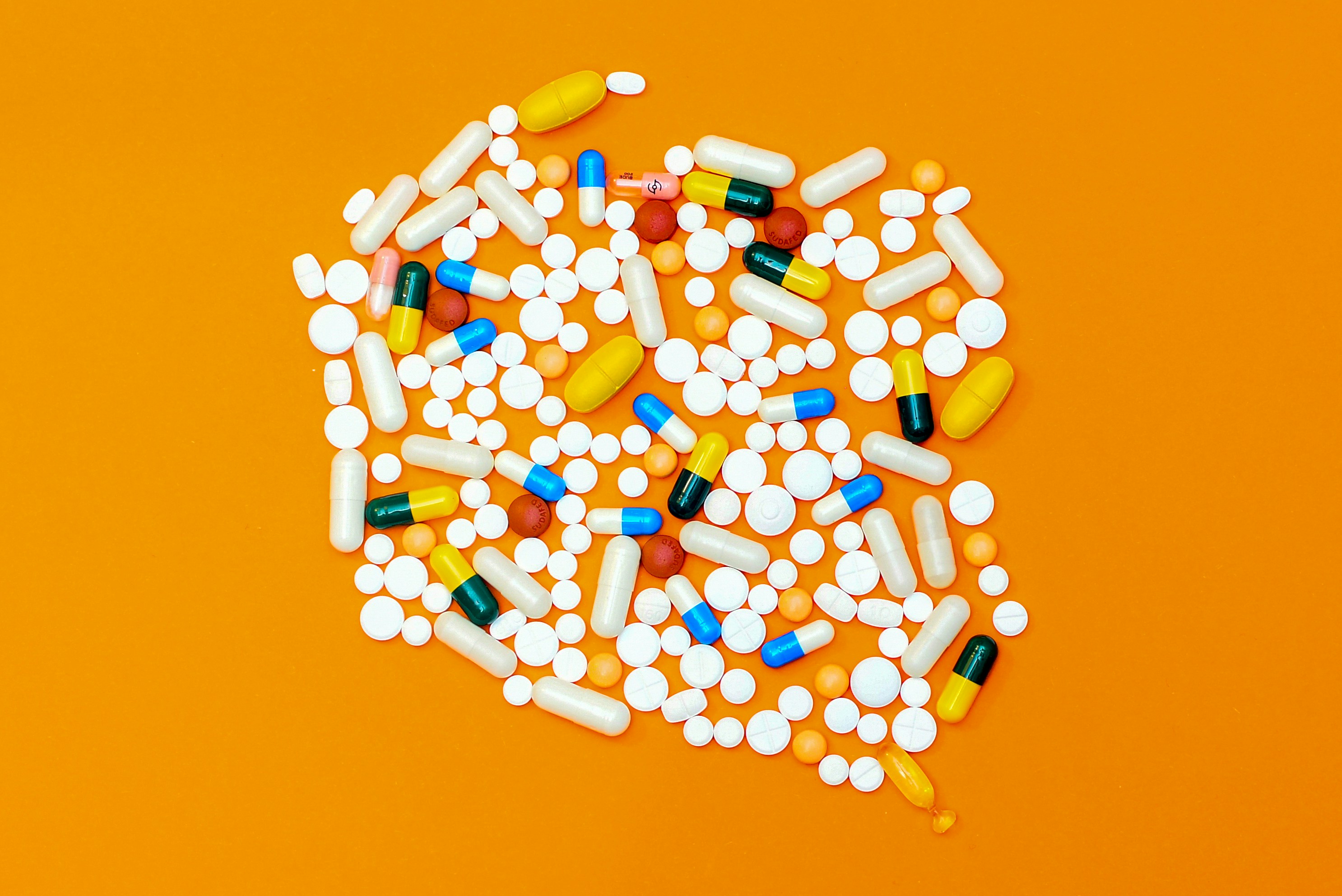
Private Label Supplements In Europe: How To Get Started
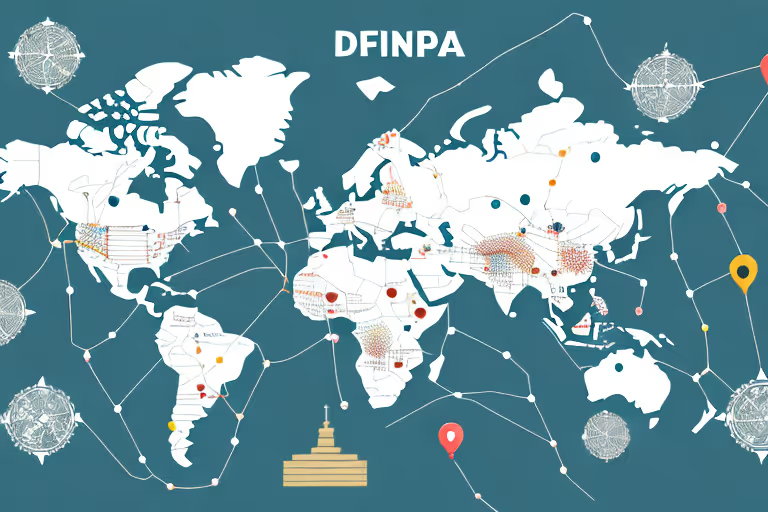