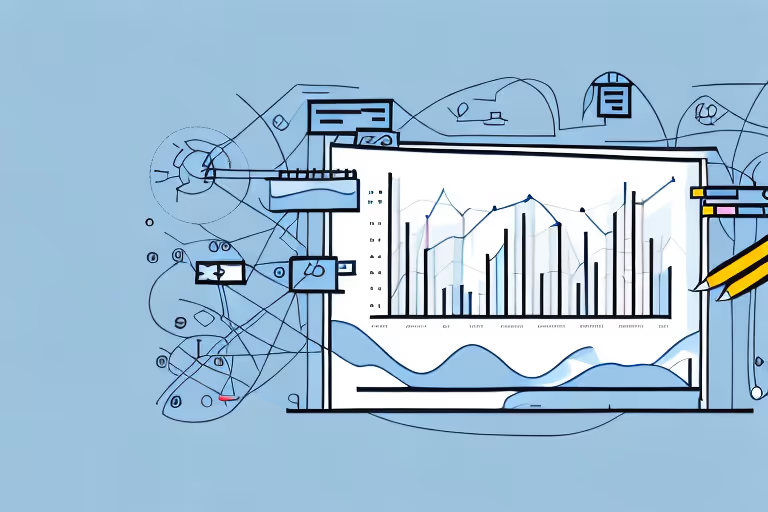
In this comprehensive guide, we will delve into the intricacies of buffer stock and provide a step-by-step approach to calculate it accurately to optimize your inventory management process.
Step-by-Step Guide to Calculate Buffer Stock
Step 1: Analyzing Historical Sales Data
The first step in calculating buffer stock is to analyze historical sales data. This data provides insights into demand patterns and seasonality. By examining past sales records, businesses can identify any recurring trends or fluctuations in demand.
For example, a retail clothing store might notice that sales of winter coats tend to increase significantly during the colder months, while sales of swimwear are higher in the summer. This analysis helps the business understand the typical demand patterns for different products throughout the year.
Using historical data, businesses can estimate the average demand and determine the standard deviation. The standard deviation serves as a measure of demand variability and helps calculate the buffer stock required to cover unexpected demand fluctuations.
By calculating the standard deviation, businesses can understand how much the actual demand typically deviates from the average. This information is crucial for determining the appropriate buffer stock level to ensure sufficient inventory availability.
Step 2: Estimating Future Demand
After analyzing historical sales data, the next step is to estimate future demand. By considering market trends, promotional activities, and other relevant factors, businesses can forecast the expected demand for their products.
This forecast will guide the calculation of buffer stock to ensure sufficient inventory levels are maintained.
Accurate demand forecasting is crucial for buffer stock calculation as it helps businesses predict the level of demand volatility and adjust the buffer stock accordingly.
For example, a smartphone manufacturer might analyze market trends and anticipate an increase in demand during the holiday season due to promotional offers and new product releases.
By accurately forecasting this surge in demand, the manufacturer can calculate the buffer stock needed to meet customer orders without experiencing stockouts.
Step 3: Assessing Supply Chain Factors
In the third step, it is essential to assess the various factors affecting supply chain dynamics. This includes evaluating supplier reliability, lead time, and any potential risks that could disrupt the supply chain.
By analyzing these factors, businesses can better anticipate any potential disruptions and adjust their buffer stock levels accordingly to minimize the impact on operations.
For instance, a manufacturing company that relies on a single supplier for a critical component might identify the supplier's history of delayed deliveries. In such cases, the business would need to maintain a higher buffer stock to compensate for the longer lead time and reduce the risk of production delays.
Step 4: Calculating the Buffer Stock
With historical sales data, projected demand, and supply chain factors assessed, businesses can now calculate the buffer stock level. This calculation considers the desired service level and the level of risk the business is willing to tolerate.
Several mathematical models, like the reorder point formula, can be used to calculate the buffer stock accurately. Utilizing these models helps businesses strike the right balance between avoiding stockouts and minimizing excessive inventory holdings.
For example, the reorder point formula takes into account the average demand, lead time, and desired service level to determine the buffer stock needed. By using this formula, businesses can calculate the exact quantity of buffer stock required to maintain a certain level of customer service while minimizing the risk of stockouts.
Overall, calculating buffer stock involves a comprehensive analysis of historical sales data, estimating future demand, assessing supply chain factors, and utilizing mathematical models to determine the appropriate buffer stock level. This process helps businesses optimize their inventory management and ensure customer satisfaction. If you're interested in further optimizing your e-commerce operations, understanding how an e-commerce warehouse works can be beneficial.
Implementing Buffer Stock in Your Inventory Management
Buffer stock is a crucial concept in inventory management that helps businesses maintain optimal inventory levels and mitigate risks. It acts as a safety net, ensuring that there is always enough stock to meet customer demand even during unexpected fluctuations in supply or demand.
Using Buffer Stock in Inventory Management Software
One way to implement buffer stock effectively is by utilizing inventory management software. Many inventory management systems offer features that allow businesses to set buffer stock levels and automate the replenishment process.
By inputting the calculated buffer stock levels into the software, businesses can ensure that the system generates alerts or automatically places orders when inventory falls below the desired level. This streamlines the procurement process and effectively manages inventory levels.
Inventory management software also provides valuable insights and analytics, enabling businesses to analyze historical data, identify trends, and make informed decisions about buffer stock levels. This data-driven approach helps optimize inventory management and improves overall operational efficiency.
Manual Buffer Stock Management
In cases where businesses do not have inventory management software, manual buffer stock management can still be effective. Although it requires more effort and attention, it allows businesses to have a hands-on approach to their inventory management.
Regularly reviewing and adjusting buffer stock levels based on demand and supply trends is vital. This involves analyzing historical sales data, monitoring market conditions, and staying updated on industry trends.
By keeping a close eye on these factors, businesses can make informed decisions about buffer stock levels and ensure that they are aligned with market demands.
Maintaining open communication with suppliers is another crucial aspect of manual buffer stock management. By building strong relationships with suppliers, businesses can stay informed about any potential disruptions in the supply chain and make necessary adjustments to buffer stock levels accordingly.
Furthermore, businesses can also consider implementing just-in-time (JIT) inventory management practices as part of their manual buffer stock management.
JIT allows businesses to minimize inventory holding costs by receiving goods from suppliers just in time for production or sale. This approach reduces the need for excessive buffer stock while still ensuring that there is enough stock to meet customer demand.
In conclusion, calculating buffer stock is a crucial aspect of effective inventory management. By understanding the key factors influencing buffer stock calculation and following a step-by-step approach, businesses can optimize their inventory levels, mitigate risks, and maintain customer satisfaction.
Factors Influencing Buffer Stock Calculation
To calculate buffer stock accurately, it is crucial to consider various factors that influence the demand and supply dynamics of a business. Understanding these factors will help determine the appropriate buffer stock level. The key factors to consider are:
Demand Variability
One crucial factor influencing buffer stock calculation is demand variability. Demand for products can fluctuate unpredictably due to changes in customer preferences, seasonal trends, or economic factors. By analyzing historical sales data and identifying demand patterns, businesses can estimate the level of demand variability and adjust their buffer stock accordingly.
For example, during the holiday season, the demand for certain products such as toys or electronics tends to increase significantly. To ensure that there is an adequate supply to meet this surge in demand, businesses may need to increase their buffer stock levels. On the other hand, during slower periods, when demand is relatively low, businesses may choose to reduce their buffer stock to avoid excess inventory and associated costs.
Supply Uncertainty
Supply uncertainty refers to the potential disruptions or delays in the supply chain that can affect the availability of inventory. Factors such as transportation issues, supplier reliability, or unexpected events can impact the supply chain. Assessing the level of supply uncertainty enables businesses to determine the adequate buffer stock needed to mitigate these risks.
For instance, if a business relies heavily on imported raw materials, it may face supply chain disruptions due to customs delays, natural disasters, or political unrest in the country of origin. To ensure a continuous supply of inventory, the business may need to maintain a higher buffer stock level to compensate for the potential supply chain uncertainties.
Lead Time
Another critical factor to consider when calculating buffer stock is lead time. Lead time refers to the time it takes for inventory to be replenished after an order is placed. Longer lead times increase the risk of stockouts during periods of high demand.
By analyzing lead time data and considering the desired service level, businesses can calculate the buffer stock required to bridge the gap between orders and replenishment.
For example, if a business experiences a lead time of two weeks to restock inventory, it needs to ensure that it has enough buffer stock to cover the demand during this period.
Without an adequate buffer stock, the business may face stockouts and potential loss of sales. By accurately estimating the lead time and considering factors such as supplier reliability and order frequency, businesses can optimize their buffer stock levels to maintain a smooth supply chain.
In conclusion, calculating buffer stock requires a thorough analysis of various factors such as demand variability, supply uncertainty, and lead time. By considering these factors, businesses can determine the appropriate buffer stock level to ensure a continuous supply of inventory and minimize the risk of stockouts.
Understanding Buffer Stock
Before we dive into the process of calculating buffer stock, let's gain a clear understanding of what it entails. Buffer stock, also known as safety stock, acts as a cushion to protect businesses against unforeseen fluctuations in demand or supply.
Having buffer stock helps businesses avoid stockouts or backorders during periods of high demand or supply disruptions. It ensures customer satisfaction and maintains smooth operations by mitigating the risks associated with stock shortages.
Buffer stock refers to the surplus inventory maintained by businesses to bridge the gap between demand and supply during unexpected fluctuations. It acts as a safety net, allowing businesses to fulfill customer orders promptly without incurring delays or disruptions.
Buffer stock is typically calculated based on historical sales data, demand variability, supply uncertainty, and lead time. By understanding these factors and implementing buffer stock effectively, businesses can optimize their inventory management process and minimize potential risks.
To fully grasp the significance of buffer stock, it is essential to recognize its impact on effective inventory management. Buffer stock provides businesses with several key benefits:
- Protects Against Unexpected Demand Surges: Buffer stock serves as a safety net, enabling businesses to meet unexpected spikes in demand promptly. It helps businesses avoid stockouts and maintain high levels of customer satisfaction.
- Mitigates Supply Uncertainty: Buffer stock acts as a buffer against supply chain disruptions, such as delays in deliveries or manufacturing issues. It ensures that businesses have stock on hand even when faced with unexpected supply disruptions.
- Enhances Flexibility: By having buffer stock available, businesses can quickly adapt to changes in customer demands or market conditions. It provides the flexibility needed to respond efficiently and maintain a competitive edge.
Buffer stock is not just a simple concept; it is a strategic tool that businesses can leverage to optimize their inventory management processes. By maintaining an appropriate buffer stock level, businesses can navigate through uncertain times and ensure a smooth flow of goods to their customers.
Calculating buffer stock involves a careful analysis of various factors, such as demand patterns, lead time variability, and desired service level. It requires businesses to strike a balance between carrying excess inventory and the cost of holding that inventory.
One method commonly used to calculate buffer stock is the use of statistical models, such as the safety stock formula or the reorder point formula. These models take into account historical data, demand variability, and lead time to determine the optimal buffer stock level.
However, it is important to note that buffer stock is not a one-size-fits-all solution. Each business must assess its unique circumstances and tailor its buffer stock strategy accordingly. Factors such as industry dynamics, customer expectations, and supply chain complexity can influence the optimal buffer stock level for a business.
Furthermore, buffer stock management is an ongoing process. As market conditions change and business dynamics evolve, businesses must regularly review and adjust their buffer stock levels to ensure they remain effective in mitigating risks and maintaining operational efficiency.
In conclusion, buffer stock plays a crucial role in inventory management by providing a safety net against unexpected fluctuations in demand or supply. It enables businesses to meet customer demands promptly, mitigate supply chain disruptions, and adapt to changing market conditions.
By understanding the importance of buffer stock and implementing effective strategies, businesses can optimize their inventory management processes and achieve long-term success.
Implementing buffer stock, whether through inventory management software or manual processes, ensures that businesses can adapt to market changes, protect against supply chain disruptions, and ultimately achieve a competitive advantage in their industry. It is an essential strategy for any business looking to optimize their inventory management practices and improve overall operational efficiency.
Looking for More Wisdom?
If you're keen to dive deeper into the world of inventory and stock management, these articles might be of interest:
- How E-commerce Warehouse Works
- How to Fulfill Orders on Shopify Dropshipping
- How to Automate a Shopify Store
These posts will provide further insights into optimizing your inventory management and understanding the intricacies of warehousing and e-commerce operations.
FAQ
Related blogs
.avif)
Private Label Supplement Manufacturers: How To Find The Right Partner
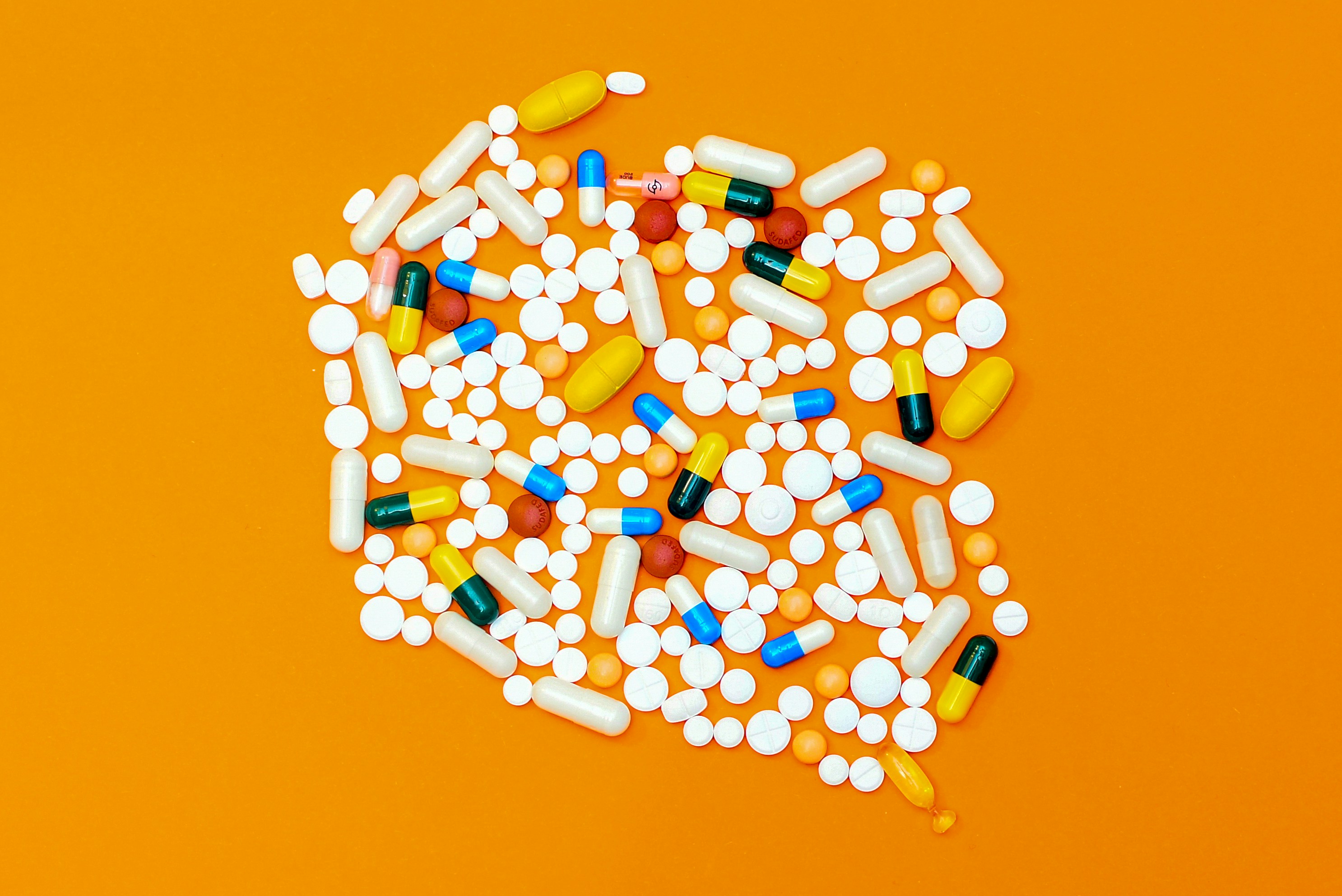
Private Label Supplements In Europe: How To Get Started
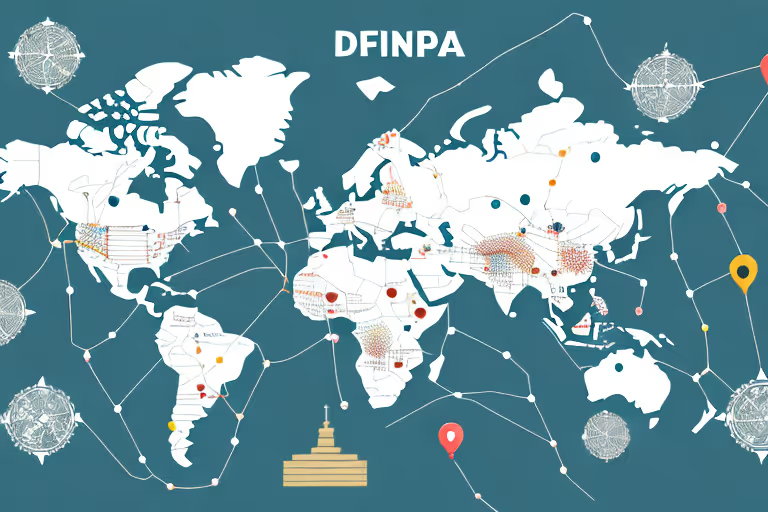