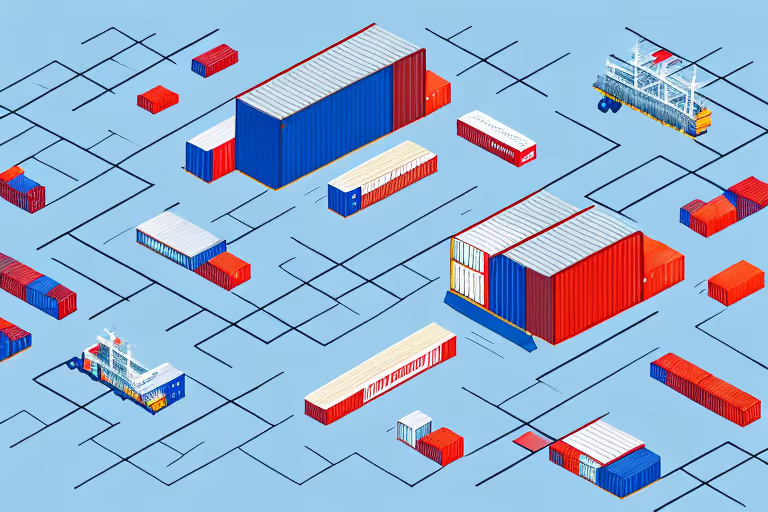
In this article, we will explore the various aspects related to the cost of 3PL services, providing you with valuable insights to help you navigate through the complexities and ultimately determine the best fit for your business needs.
Understanding 3PL Service Costs: A Comprehensive Guide
In today's dynamic business landscape, companies of all sizes are turning to third-party logistics (3PL) providers to enhance their supply chain efficiency and focus on core competencies.
However, understanding the typical cost for 3PL services can be a complex task, as it varies depending on several factors. In this blog, we will delve into the key factors that influence 3PL pricing and provide insights into the typical costs associated with outsourcing logistics to a 3PL provider.
1. Services Offered:
The cost of 3PL services primarily depends on the scope of services offered. Basic 3PL services, such as warehousing and transportation, tend to have lower costs compared to more comprehensive solutions like end-to-end supply chain management or value-added services.
2. Warehousing Space:
3PL providers charge for the amount of warehouse space utilized by a company. The cost varies based on the size of the space, location, and duration of usage. Additional services like inventory management and order fulfillment may incur additional charges.
3. Transportation:
Transportation costs are a significant component of 3PL pricing. The mode of transportation (air, ocean, road, or rail), distance traveled, and shipment size influence the overall transportation costs.
4. Order Volume:
The volume of orders handled by a 3PL provider can impact pricing. Larger order volumes may lead to economies of scale and potentially lower costs per unit.
5. Technology Integration:
Advanced technology and software integration can improve supply chain visibility and efficiency. However, integrating with a 3PL provider's systems or using their technology solutions may lead to additional costs.
6. Value-Added Services:
Additional services, such as kitting, assembly, labeling, and packaging customization, may come with extra charges. These value-added services contribute to higher 3PL costs but can add significant value to a company's logistics operations.
7. Seasonal Demand:
Fluctuations in demand throughout the year can impact 3PL costs. Providers may adjust pricing to accommodate seasonal spikes in demand or offer flexible pricing models.
8. Industry and Geography:
The industry in which a company operates and its geographical location can also influence 3PL pricing. Certain industries, such as pharmaceuticals or perishable goods, may have specific compliance and handling requirements that affect costs.
9. Contract Length:
Long-term contracts with 3PL providers often result in more favorable pricing terms. Companies that commit to longer partnerships may receive cost incentives.
The typical cost for 3PL services varies significantly depending on the specific needs and requirements of a company. While it may seem complex to determine the exact pricing, understanding the key factors that influence 3PL costs can help businesses make informed decisions.
By assessing the scope of services required, warehouse space, transportation needs, technology integration, and other essential factors, companies can find a 3PL provider that aligns with their logistics objectives and budget.
Collaborating with a reputable 3PL partner can lead to improved supply chain efficiency, reduced costs, and enhanced customer satisfaction, ultimately driving business success in today's competitive market.
Factors Influencing the Cost of 3PL Services
Now that we understand the basics of 3PL services, let's explore the factors that influence the cost of these services. By considering these factors, you can gain insights into how the pricing structure is determined and make informed decisions about managing your logistics costs.
The Size and Complexity of Operations
One of the key factors that influence the cost of 3PL services is the size and complexity of your operations. Providers often consider factors such as the number of SKU's (stock-keeping units) handled, order volumes, and the number of locations involved.
Larger operations with more intricate requirements may require additional resources and customization, leading to higher costs.
For example, if your business deals with a wide range of products, each with its own SKU, the 3PL provider will need to allocate more time and resources to manage and track these different items.
This increased complexity can result in higher costs as the provider needs to invest in advanced inventory management systems and hire skilled staff to handle the diverse range of products.
In addition, the volume of orders processed by the 3PL provider can also impact the cost. Higher order volumes may require additional labor, equipment, and technology to ensure efficient and timely order fulfillment. This increased demand for resources can contribute to higher pricing for the services rendered.
Geographic Scope of Services
The geographic scope of services is another crucial factor to consider when estimating your 3PL costs. If your operations span multiple regions, a provider with a global reach may be necessary, which can result in higher costs due to increased transportation and warehousing expenses.
When working with a global 3PL provider, you need to consider the costs associated with international shipping, customs clearance, and compliance with different regulations in various countries. These additional logistical challenges can significantly impact the overall cost structure.
On the other hand, a local or regional provider might offer cost advantages for businesses operating within a specific geographical area. By focusing on a smaller geographic scope, the provider can optimize their operations and minimize transportation costs.
This localized approach can result in more competitive pricing for businesses that do not require extensive international logistics support.
Specialized Service Requirements
Businesses with specialized service requirements, such as temperature-controlled storage or hazardous materials handling, will naturally incur higher costs due to the additional expertise, technology, and equipment needed to meet these specific needs.
For instance, if your products require temperature-controlled storage to maintain their quality and integrity, the 3PL provider will need to invest in specialized warehouses equipped with advanced cooling or heating systems.
These facilities come with higher operating costs, which are passed on to the businesses availing of the service.
Similarly, the handling of hazardous materials involves strict safety protocols, specialized training for staff, and compliance with various regulations. These additional requirements increase the complexity and cost of the 3PL services provided.
It's crucial to carefully evaluate the level of specialization required and assess its impact on the overall cost structure. While specialized services may come with higher costs, they are essential for businesses that deal with sensitive or regulated products, ensuring compliance and customer satisfaction.
Breakdown of Typical 3PL Costs
Now that we have explored the key factors influencing the cost of 3PL services, let's delve into the specific cost components you can expect when partnering with a 3PL provider.
When it comes to partnering with a third-party logistics (3PL) provider, understanding the breakdown of costs is crucial. It helps you make informed decisions and ensures that you have a clear understanding of where your money is going.
In this section, we will explore the different cost components that make up the overall expenses of working with a 3PL.
Warehousing Costs
Warehousing costs are a significant component of 3PL expenses. These costs typically include rent or lease fees for warehouse space, utilities, labor costs, and equipment expenses.
The specific warehousing costs can vary depending on factors such as the size of the facility, location, and additional services required, such as value-added activities like packaging or labeling.
When it comes to warehouse space, the size and location play a crucial role in determining the cost. Larger facilities with more storage capacity generally come with higher rental fees.
The location of the warehouse also affects the cost, as warehouses situated in prime locations or near transportation hubs tend to have higher lease rates. Additionally, the type of equipment required and the complexity of the operations can add to the overall warehousing costs.
Transportation Costs
Transportation costs comprise expenses related to the movement of goods between locations. These costs can include shipping fees, fuel costs, tolls, and driver wages.
The exact transportation costs depend on factors like the distance traveled, mode of transportation (such as road, rail, air, or sea), and any special requirements like expedited shipping or specialized handling.
When it comes to transportation costs, the distance between the origin and destination is a key factor. Longer distances generally result in higher shipping fees and fuel costs.
The mode of transportation also plays a significant role in determining the cost. For example, air freight is typically more expensive than road or rail transportation. Specialized handling requirements, such as temperature-controlled shipping or hazardous material handling, can also increase transportation costs.
Inventory Management Costs
Inventory management costs encompass activities related to tracking, storing, and managing stock levels. These costs can include expenses associated with inventory tracking systems, inventory audits or cycle counts, and managing stock obsolescence or returns.
The complexity and accuracy of inventory management requirements impact the costs incurred in this area.
Effective inventory management is crucial for businesses to maintain optimal stock levels and meet customer demands. Implementing inventory tracking systems and conducting regular audits or cycle counts incur costs.
The complexity of the inventory management requirements, such as handling a wide range of SKUs or managing perishable goods, can also contribute to the overall expenses in this area. Additionally, managing stock obsolescence or processing returns can add to the inventory management costs.
Value-added Services Costs
Value-added services refer to additional activities provided by the 3PL, such as kitting, labeling, product customization, or returns processing. These services can offer added convenience or value to your customers but typically come at an additional cost.
The exact cost of value-added services can vary depending on the complexity and volume of these activities.
Value-added services can enhance the overall customer experience and provide a competitive edge. However, it's important to consider the cost implications. Services like kitting, where different products are bundled together, or labeling, where customized labels are applied to products, incur additional expenses.
Similarly, product customization or personalization may require extra resources, resulting in higher costs. Returns processing, including inspecting returned items and restocking them, can also contribute to the overall expenses in this category.
How to Estimate Your 3PL Costs
Estimating your 3PL costs accurately is crucial to effectively manage your logistics budget. Let's explore the fundamental aspects of estimating your 3PL costs.
Understanding Pricing Models in 3PL
3PL providers typically use different pricing models to charge for their services. Common models include transaction-based pricing, where costs are based on specific activities performed, and volume-based pricing, where costs are determined by the overall volume of goods handled.
Understanding the pricing models used by potential 3PL partners will help you align your cost estimates more accurately.
Cost Calculation Examples
Calculating 3PL costs can be complex, but let's consider a couple of examples to illustrate how the different factors discussed above can impact your costs.
For a small e-commerce business with a limited product range and local operations, the costs may be relatively lower compared to a large multinational corporation with extensive global operations and highly specialized requirements.
By analyzing and comparing different scenarios considering your specific business needs, you can develop a more accurate estimate of your 3PL costs.
Conclusion
In conclusion, determining the typical cost for 3PL services requires a comprehensive analysis of various factors such as the size and complexity of operations, geographic scope, and specialized service requirements.
By understanding these factors and their impact on the key cost components, including warehousing, transportation, inventory management, and value-added services, businesses can estimate their 3PL costs more effectively. Remember, each business is unique, and finding the right balance between cost and service quality is essential when choosing a 3PL provider.
Looking for More Insights?
Expand your understanding of logistics and e-commerce with these insightful articles:
- How to Start a Fulfillment Warehouse
- Is It Possible to Become a Multi-Millionaire Dropshipping?
- Do You Need a Business License to Sell on Shopify?
By delving into these resources, you'll gain a comprehensive view of the challenges and opportunities in the e-commerce landscape.
FAQ
Related blogs
.avif)
Best Supplement Manufacturers in the USA: How to Find the Right Partner
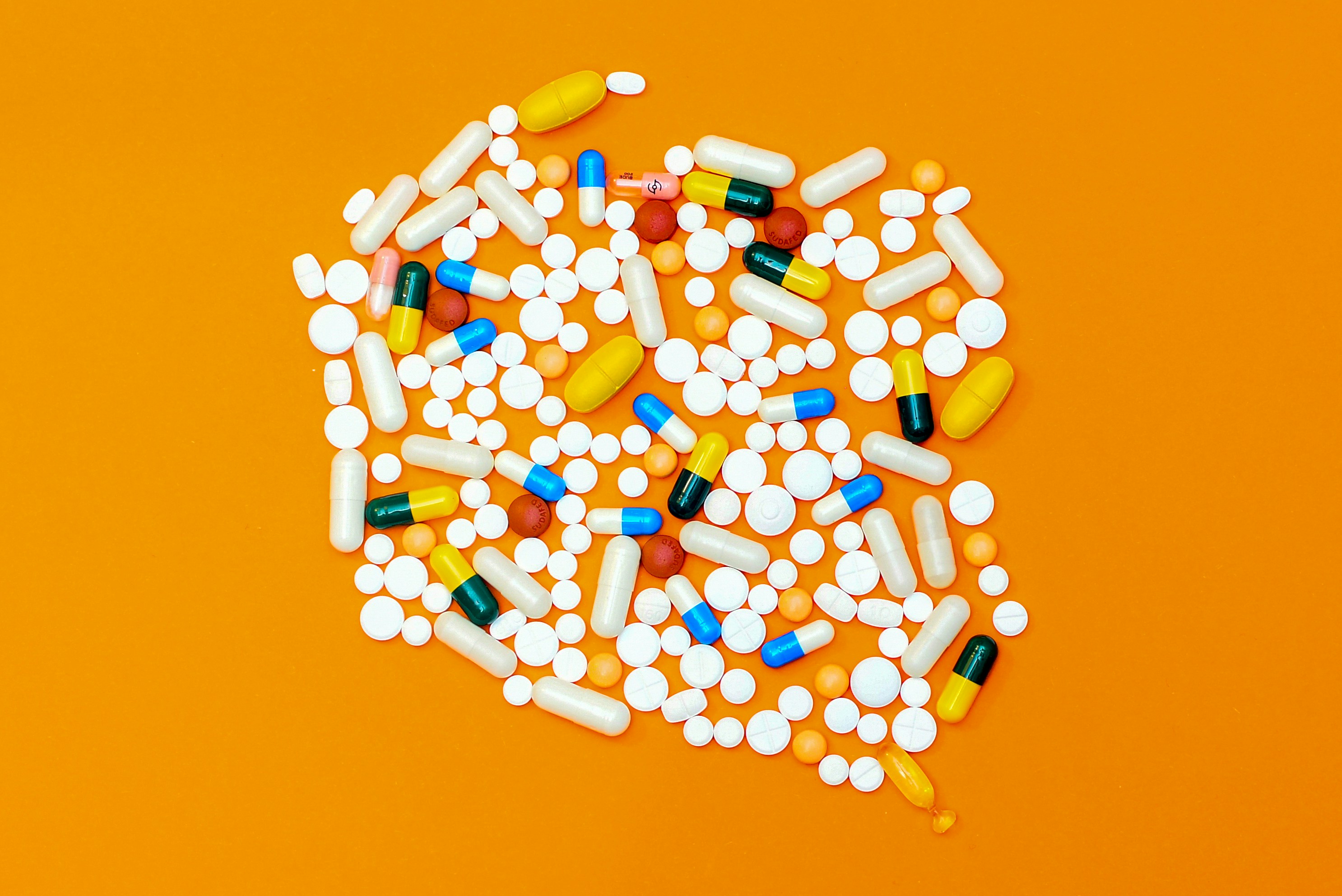
Private Label Supplements In Europe: How To Get Started
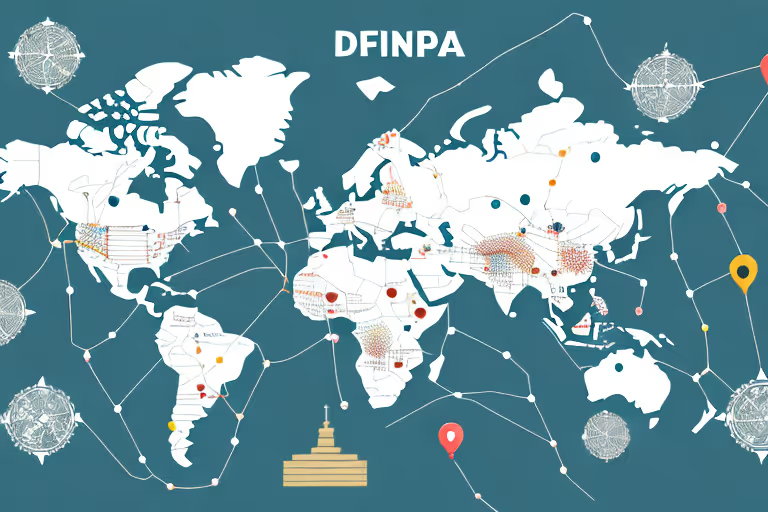