.avif)
From the role of a shipping and receiving warehouse to the importance of an efficient layout and the benefits of implementing warehouse management systems, this article will guide you through the key components of how a shipping and receiving warehouse should operate.
Implementing warehouse management systems
In today's digital age, warehouse management systems (WMS) play a pivotal role in streamlining operations and optimizing efficiency. These software solutions provide a centralized platform for managing inventory, processing orders, and tracking shipments.
Let's explore the benefits of implementing a WMS and discuss the factors to consider when choosing the right system for your warehouse.
Benefits of warehouse management systems
Warehouse management systems offer a myriad of benefits to shipping and receiving warehouses. They provide real-time visibility into inventory levels, enabling accurate demand forecasting and efficient order fulfillment.
With features like barcode scanning and automated workflows, WMS help reduce errors and increase productivity, ultimately leading to improved customer satisfaction.
Furthermore, WMS enable data-driven decision-making by generating detailed reports and analytics. These insights can be used to identify areas for improvement, optimize warehouse processes, and make informed strategic decisions.
With a WMS in place, you can gain a competitive edge by delivering faster, more reliable, and cost-effective shipping and receiving services.
Choosing the right warehouse management system
When selecting a warehouse management system for your operation, it's important to consider your specific needs and budget. Look for a system that integrates seamlessly with your existing technology infrastructure and offers scalability to accommodate future growth.
Evaluate the system's user-friendliness, training and support options, and compatibility with your preferred hardware devices.
Additionally, pay attention to the system's features and functionality. Does it support advanced inventory tracking methods like lot or serial number tracking? Can it handle multiple warehouse locations or handle complex order routing rules?
By carefully assessing your requirements and comparing different WMS providers, you can find the system that best aligns with your operation's unique needs.
Understanding the shipping process
Efficient shipping processes are essential to ensure that products reach customers in a timely and cost-effective manner. From order preparation to final delivery, let's explore the stages of the shipping process and discuss some best practices for optimizing this crucial aspect of warehouse operations.
Stages of the shipping process
The shipping process typically involves several stages, each requiring careful coordination and attention to detail.
- It begins with order processing, where orders are verified, packed, and prepared for shipment.
- Next, carriers are selected based on factors such as shipping speed, destination, and cost. Once packages are ready for transport, they undergo labeling and documentation to comply with regulatory requirements.
- Finally, packages are handed off to the selected carriers for delivery to the end customer.
Best practices for efficient shipping
To streamline the shipping process and minimize delays, it's crucial to establish standardized procedures and implement best practices. Consider implementing automated order processing systems and barcode scanning to ensure accurate order picking and packing.
Invest in shipping software that integrates with carriers' systems to generate shipping labels and streamline the documentation process.
Additionally, negotiate favorable shipping rates with carriers and explore options like shipping consolidators or fulfillment centers to optimize shipping costs.
Monitor carrier performance and establish key performance indicators to continuously evaluate and improve shipping processes.
Regularly review and update shipping policies and procedures to keep up with industry changes and customer expectations.
Mastering the receiving process
Efficient receiving processes are crucial for maintaining accurate inventory records and ensuring the seamless flow of goods within a warehouse. From checking in incoming shipments to inspecting and properly storing inventory, let's dive into the steps involved in the receiving process and explore strategies for streamlining this vital operation.
Steps in the receiving process
The receiving process is a multi-step procedure that starts the moment a shipment arrives at the warehouse's doorstep.
- It begins with unloading the goods and verifying the quantities received against the shipping documents.
- The next step involves inspecting the products for any damage or quality issues and comparing them to the purchase order specifications.
- Once the goods have been inspected, they are properly labeled, counted, and put away in their designated storage locations.
How to streamline the receiving process
To optimize the receiving process and minimize inefficiencies, it's important to establish clear protocols and procedures. Train receiving staff on proper inspection techniques and ensure they have the necessary tools, such as scales, measuring devices, and quality control checklists, to perform their tasks accurately and efficiently.
Consider implementing barcoding or RFID systems to facilitate inventory tracking and automate data entry during the receiving process. This reduces the likelihood of manual errors and speeds up the overall process. Regularly review and update receiving procedures to incorporate industry best practices and accommodate changing business needs.
Understanding the basics of a shipping and receiving warehouse
Before we dive into the intricacies of warehouse management, it's important to grasp the fundamental concepts of a shipping and receiving warehouse. Put simply, this type of facility serves as a hub for receiving incoming products, storing inventory, and fulfilling customer orders through efficient shipping processes.
From warehouses in bustling urban centers to sprawling spaces in industrial areas, the operations within these facilities form the backbone of the supply chain.
Let's take a closer look at the role of a shipping and receiving warehouse and the key components that make it a well-oiled machine.
The role of a shipping and receiving warehouse
At its core, a shipping and receiving warehouse plays a vital role in the movement of goods from suppliers to customers. It serves as a central location where products are received, sorted, stored, and then ultimately shipped to their final destinations.
This process involves a range of activities, such as inspecting incoming shipments, organizing inventory, picking and packing orders, and coordinating transportation logistics. Each step is crucial to ensure that the right products reach the right customers in a timely manner.
When a shipment arrives at the warehouse, it undergoes a thorough inspection to verify its quality and quantity. This step is essential to identify any damaged or missing items and resolve any discrepancies with the supplier.
Once the inspection is complete, the products are sorted and organized based on their characteristics, such as size, weight, and fragility. This careful organization allows for efficient storage and retrieval, minimizing the time it takes to fulfill customer orders.
When it comes to fulfilling orders, the warehouse staff follows a meticulous process of picking and packing. They navigate through the aisles, locating the required items, and ensuring they are packaged securely for transportation.
This attention to detail helps prevent any damage during transit and ensures that the products arrive at the customer's doorstep in pristine condition.
Coordinating transportation logistics is another critical aspect of a shipping and receiving warehouse. This involves working closely with transportation partners to schedule pickups, track shipments, and optimize routes.
By collaborating effectively, the warehouse can ensure that the products are delivered to customers on time, meeting their expectations and fostering positive customer experiences.
Key components of a warehouse operation
A well-operated shipping and receiving warehouse relies on several key components to keep operations running smoothly. First and foremost, inventory management is essential.
Keeping track of stock levels, replenishing supplies when needed, and conducting regular audits are vital for maintaining accurate records and avoiding stockouts or overstock situations.
By implementing robust inventory management practices, warehouses can optimize their storage space, reduce carrying costs, and improve overall efficiency.
Additionally, effective communication and collaboration among warehouse staff, suppliers, and transportation partners are crucial for minimizing errors and achieving optimal efficiency.
Clear lines of communication ensure that everyone involved in the supply chain is on the same page, enabling swift problem-solving and preventing any bottlenecks that could disrupt operations.
In order to streamline operations, many warehouses today also utilize technology-driven solutions such as barcode scanners, RFID systems, and warehouse management systems (WMS).
These tools automate processes, provide real-time insights into inventory levels and order statuses, and enable data-driven decision-making. By harnessing the power of technology, warehouses can greatly enhance productivity and accuracy, driving overall operational success.
Barcode scanners and RFID systems, for example, enable quick and accurate tracking of inventory. They eliminate the need for manual data entry, reducing the risk of human error and saving valuable time.
Warehouse management systems (WMS) serve as a centralized platform that integrates various functions, including inventory management, order processing, and reporting. This comprehensive software enables warehouse managers to monitor operations, analyze performance metrics, and make data-backed decisions to optimize efficiency and customer satisfaction.
In conclusion, a shipping and receiving warehouse is a complex ecosystem that plays a crucial role in the supply chain. By understanding its fundamental concepts and implementing key components such as inventory management, effective communication, and technology-driven solutions, warehouses can operate efficiently, meet customer demands, and contribute to the overall success of businesses.
Setting up an efficient warehouse layout
One of the foundational aspects of a well-operated shipping and receiving warehouse is an efficient layout. A thoughtfully designed warehouse layout maximizes space utilization, minimizes travel distance, and optimizes workflow.
Let's explore why a well-designed layout is so important and discover some tips for creating an effective configuration.
Importance of warehouse layout
The layout of a warehouse impacts every aspect of its operation, from the speed and accuracy of order fulfillment to the safety of workers. A poorly designed layout can result in wasted space, inefficient movement of goods, and increased risk of accidents.
On the other hand, a strategically planned layout can enhance productivity, improve inventory control, and create a safer working environment.
Imagine a warehouse where items are scattered randomly, without any logical organization. Workers would spend valuable time searching for items, leading to delays in order fulfillment and decreased efficiency.
In contrast, a well-organized layout ensures that similar items are grouped together, making it easier for workers to locate and retrieve them quickly. This not only saves time but also reduces errors and improves customer satisfaction.
Moreover, an efficient warehouse layout minimizes travel distance for workers. By strategically placing workstations, shelving units, and equipment, you can significantly reduce the time spent walking or driving between different areas of the warehouse.
This streamlined movement not only increases productivity but also reduces fatigue and the risk of injuries caused by excessive physical exertion.
Tips for designing an effective layout
When designing a warehouse layout, consider the specific needs of your operation and aim to strike a balance between functionality and flexibility. Start by analyzing your inventory flow and identify areas where bottlenecks may occur. Utilize tools like flow charts or process maps to visualize the movement of goods within the facility.
For example, if you notice that certain items are frequently requested together, it would be wise to store them in close proximity to each other. This practice, known as zone picking, reduces the time required to gather multiple items for an order, increasing overall efficiency.
Additionally, you can implement cross-docking, a technique where incoming goods are directly transferred to outbound vehicles without being stored, to eliminate unnecessary storage and handling steps.
Next, determine the optimal placement of workstations, shelving units, and equipment to minimize travel distance and promote efficient order picking and product replenishment.
Consider factors such as item popularity and storage requirements when organizing inventory locations. High-demand items should be easily accessible, while slower-moving items can be placed in less accessible areas to optimize space utilization.
Furthermore, prioritize safety by ensuring clear pathways, properly maintaining equipment, and implementing proper signage and lighting throughout the facility. By minimizing potential hazards and providing a well-lit environment, you can reduce the risk of accidents and create a safer working environment for your employees.
Remember that designing a warehouse layout is an ongoing process. As your business evolves and your inventory changes, regularly review and adjust your layout to accommodate new requirements and optimize efficiency. By continuously improving your warehouse layout, you can stay ahead of the competition and ensure smooth operations.
FAQ
Related blogs
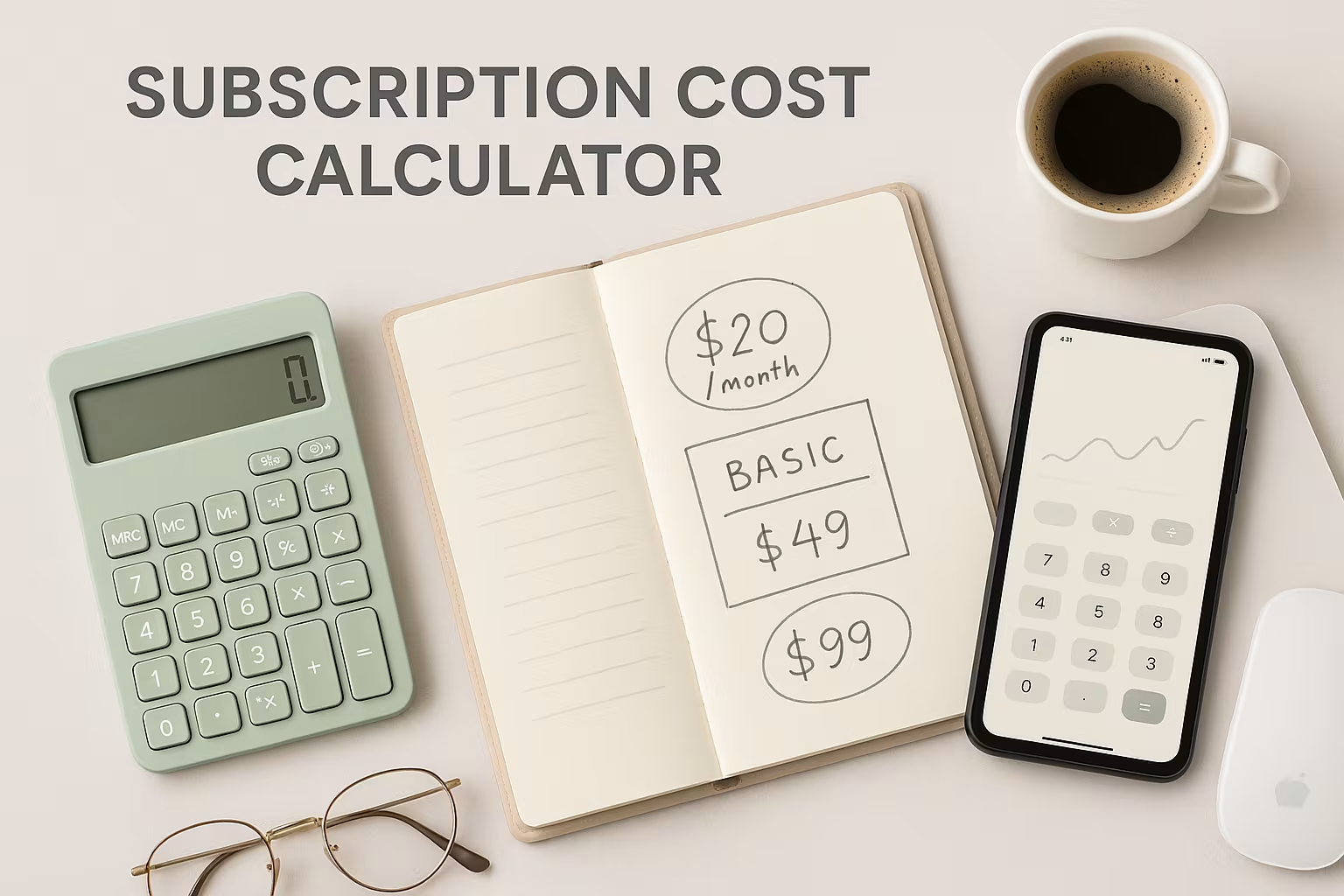
Subscription Cost Calculator: The Tool Every E-commerce Brand Needs
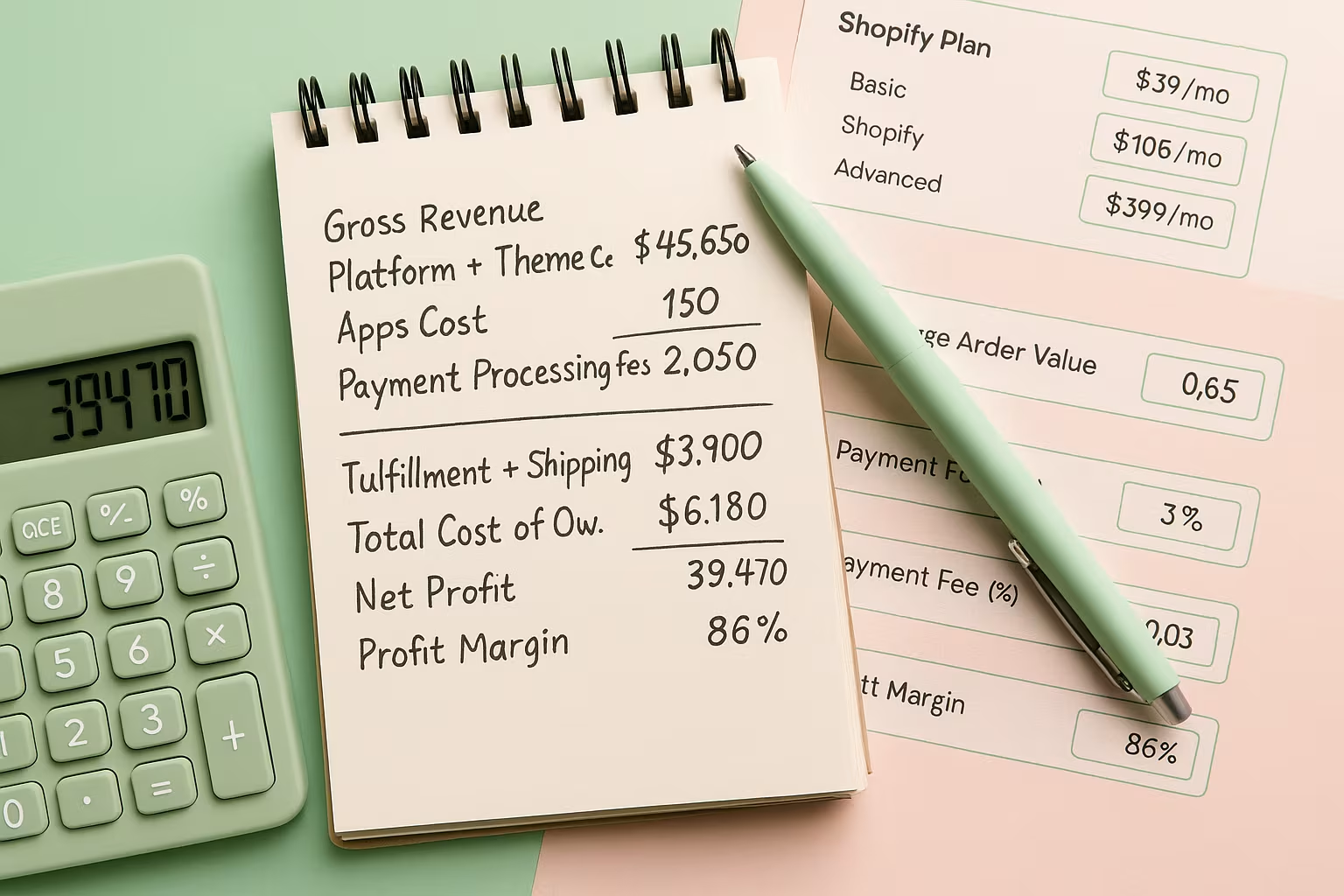